Na manutenção de qualquer instalação, tomar como base o diagnóstico prévio dos equipamentos e sistemas que o conformam, genericamente denominado de manutenção baseada em condição (MBC), é uma estratégia de manutenção que tem oferecido a muitas empresas dois objetivos fundamentais relativamente à manutenção: redução de custos e aumento na disponibilidade de equipamentos para produção. Para algumas empresas, brindar esses resultados de maneira rápida supõe ingressar no caminho da viabilidade e da competitividade, enquanto para outras significa obter um benefício maior daquele que obteriam se basearam a manutenção em outras estratégias, como na correção simples de avarias ou somente nas recomendações mínimas informadas pelo fabricante do equipamento. Esta matéria revê os fundamentos principais do MBC e suas vantagens em comparação com outras estratégias.
Os custos de manutenção em instalações de médio ou grande porte representam entre 2 e 3% do custo anual total da instalação. Isso significa que uma empresa, cuja reposição de ativos foi avaliada em 100 milhões de euros, pode considerar entre dois e três milhões de euros anuais incluindo pessoal, contratos com empresas externas e materiais. Para muitas empresas, esse custo é perfeitamente suportável, porque representa pouco se comparado com suas receitas. Mas, para outras, significa ‘lutar’ para serem mais competitivas ou até batalhar pela própria sobrevivência, e são obrigadas a reduzir custos. Uma via ‘dura’ de redução é atribuir um orçamento pequeno à manutenção e que o próprio departamento tente gerenciá-lo da melhor forma possível. Este tipo de soluções, geradas de maneira cega pela área financeira, não apresentaram bons resultados e o único que conseguem é demorar custos que futuramente podem ser maiores que os que é necessário economizar no curto prazo. Vale lembrar que tudo aquilo que for feito hoje, na gestão da manutenção de uma instalação, oferecerá resultados pelo menos seis meses depois.
Porém, há formas mais inteligentes e eficazes de atingir o mesmo efeito, isto é, de reduzir os custos anuais de manutenção sem sacrificar a vida útil e nem incrementar os custos no futuro. Uma destas opções é basear a manutenção na análise prévia dos equipamentos. Uma manutenção que toma como base a condição reduz custos até montantes que variam entre 1 e 1,5 do custo da instalação, sem comprometer a disponibilidade, a produção ou aumentar a possibilidade de ocorrência de sinistros. De fato, a disponibilidade e a produção aumentam geralmente e a sinistralidade diminui.
Para entender corretamente o que é isto e quais são suas consequências, é necessário rever rapidamente outras opções existentes. A primeira delas, utilizada por muitas empresas e que costuma oferecer resultados pouco satisfatórios, tanto em termos de custo quanto de disponibilidade, e até do ponto de vista da sinistralidade, é basear a manutenção na solução das avarias que vão acontecendo.
Uma manutenção que toma como base a condição reduz custos até montantes que variam entre 1 e 1,5 do custo da instalação, sem comprometer a disponibilidade, a produção ou aumentar a possibilidade de ocorrência de sinistros.
Manutenção baseada na solução de avarias
É uma estratégia puramente reativa, que simplesmente espera que as diversas máquinas que integram a instalação apresentem falhas para poder agir e corrigir. Assim, a produção perde confiabilidade e o custo pode ser incerto, sendo muito variável de um ano para outro, porque depende das avarias que possam acontecer. Certamente, quando a avaria se produz costuma ser muito mais grave que se os sintomas tivessem sido detectados antes.
Manutenção baseada na vida útil dos equipamentos
Juntamente com esta estratégia corretiva, está a possibilidade de basear somente a manutenção nas recomendações dos fabricantes. Estas recomendações costumam orientar a manutenção para uma estratégia sistemática, isto é, para a realização de uma série de tarefas por horas de funcionamento ou períodos de tempo naturais, que em muitos casos representam substituir determinados componentes por terem alcançado o final de sua vida útil. Assim, estima-se que um rolamento dure uma quantidade ‘X’ de horas, que um filtro deve ser trocado a cada certo período de tempo ou que é preciso desmontar e substituir peças internas de determinados componentes de grande profundidade (turbinas a vapor e gás, motores alternativos, bombas, compressores, etc.), porque atingiram um número de horas de operação ou porque foi estabelecido que, a cada certo tempo, o equipamento de instalação deve ser submetido a uma grande intervenção.
Com o MBC, o número de paradas causadas por avarias produzidas se reduz
Manutenção baseada em condição (MBC)
A estratégia da manutenção baseada em condição, ou MBC, foge das abordagens de substituição sistemática de elementos por alcançar o final da vida útil estimada a priori pelo fabricante. Contudo, a MBC propõe que os equipamentos devem receber intervenção só na existência de algum sintoma de degradação. No século XXI, há muitas técnicas que possibilitam avaliar se um equipamento sofreu degradação e, a maioria delas, são técnicas não invasivas, isto é, dificilmente podem provocar danos pelo fato de serem implementadas. Além disso, permitem determinar se os componentes dos equipamentos realmente esgotaram sua vida útil. Isto permite minimizar o número de intervenções efetuadas nos equipamentos, pois só são realizadas naqueles que realmente precisam e quando apresentam quaisquer sintomas de degradação em uma fase precoce.
Técnicas de diagnóstico
A MBC costuma ser associada ao que durante muito tempo se denominou “manutenção preditiva’”, isto é, uma série de técnicas que tentam estabelecer uma relação entre determinadas variáveis físicas e a degradação apresentada por uma máquina, tudo medido com equipamentos de certo valor e complexidade. Apesar de que realmente este tipo de técnicas (análise de vibrações, termografias, inspeções boroscópicas, análise de óleo, análise por ultrassom, etc.) resultam muito úteis e quase imprescindíveis em uma MBC, nem de longe são as mais importantes nem as que mais incidências descobrem em uma instalação.
É possível estabelecer que as técnicas de diagnóstico, que a MBC toma como base, podem ser agrupadas em quatro categorias:
- RODADAS DE OPERAÇÃO: As rodadas de operação são uma série de atividades, geralmente de inspeção, realizadas pelos operadores da planta. Basicamente, consistem em inspeções sensoriais e testes de funcionamento. A frequência é elevada e podem ser realizadas de forma diária ou mesmo a cada poucas horas. Os operadores descobrem quase 40% dos problemas em uma fase precoce, já que muitas das ocorrências nas máquinas podem ser detetáveis à simples vista.
A MBC permite manter a boa condição de uso muito além da vida útil que, em geral, costuma ser estabelecida para equipamentos industriais
2. INSPEÇÕES SENSORIAIS DETALHADAS As inspeções sensoriais detalhadas são aquelas realizadas por especialistas em manutenção (mecânicos, elétricos e instrumentistas), com fortes conhecimentos na matéria. Apesar de se tratarem fundamentalmente de testes de funcionamento e de inspeções sensoriais, às vezes envolvem paradas de máquinas ou determinadas desmontagens. Em geral, incluem todas as tarefas das rotas de operação, além de outras que não podem ser realizadas pelos operadores. A frequência de cada tarefa é variável, apesar de que há uma frequência que se repete muitas vezes neste tipo de inspeções: a frequência trimestral. Isto como consequência de que o período de incubação de muitas avarias que acontecem em uma instalação é superior a três meses. Então, com inspeções trimestrais é possível determinar o começo da gestação de certos problemas.
3. MEDIÇÕES COM EQUIPAMENTOS OFFLINE A análise com equipamentos de medição offline tenta estabelecer uma relação entre determinadas variáveis físicas (vibração, temperatura superficial, geração de determinado som, etc.) e o estado de degradação apresentado por uma máquina. Tradicionalmente foram denominadas técnicas de manutenção preditiva, apesar de que o conceito de ‘manutenção preditiva’ em verdade não existe como tal, pois a aplicação dessas técnicas não permite predizer com exatidão quando uma avaria será gerada, bem como realmente não é manutenção, porque não compensa a degradação que o tempo e o uso provocam nos materiais. Estas técnicas, cuja frequência muitas vezes é também trimestral, referem-se às análises de vibrações, termografias, inspeções boroscópicas, análise por ultrassom, etc., e têm a característica comum de que o técnico levará os equipamentos, posteriormente irá montá-los, obterá as medições e tirará suas conclusões a partir dessas observações.
4. ANÁLISE DE DADOS ONLINE Hoje em dia, os equipamentos estão muito monitorados e instrumentados e, além disso, contam com sensores para captar online muitos parâmetros de funcionamento. A partir da leitura destes parâmetros de funcionamento, e considerando que há variáveis que devem ser estabelecidas em uma faixa estática e outras em faixas dinâmicas, é possível determinar se um equipamento funciona ou não corretamente.
Vantagens em comparação com outras estratégias
Como detalhado neste artigo, a manutenção baseada em condição pode proporcionar grandes vantagens à manutenção da maioria das instalações que conhecemos. Essas vantagens se relacionam basicamente com a redução de custos, já que se em uma estratégia sistemática os custos não costumam ser inferiores a 2% ou 3% do valor total da instalação, para uma manutenção baseada em condição é muito normal obter índices entre 1 e 1,5% do custo total da instalação, incluindo pessoal, materiais e contratos de serviços com outras empresas.
A segunda das grandes vantagens se refere à disponibilidade, porque o número de paradas de manutenção sistemática se reduz drasticamente. Também diminui o número de paradas causadas por avarias produzidas pela realização de inspeções desnecessárias: cada vez que um equipamento é aberto põe em risco o equipamento, devido a que podem acontecer avarias que o equipamento não apresentava antes de abertura.
A terceira e última vantagem está relacionada com a vida útil da instalação: um equipamento bem monitorado, com informação sobre seu estado e intervido a tempo após a detecção do problema, conserva sua boa condição de uso muito além da vida útil que costuma ser estabelecida para equipamentos industriais.
Perfil do autor
Santiago García Garrido
Diretor Técnico RENOVETEC
Santiago García Garrido é licenciado em ciências químicas e doutorado em Engenharia Naval. Ele foi o diretor da usina termelétrica de ciclo combinado de San Roque, a primeira desse tipo em funcionamento na Espanha, e ocupou vários cargos de responsabilidade em empresas como Duro Felguera e Gas Natural. Atualmente é diretor técnico da RENOVETEC e presidente da Associação Espanhola de Engenharia de Manutenção.
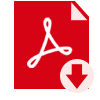