O papel que desempenhará o hidrogênio verde no contexto da estratégia da Comissão Europeia para reduzir as emissões de gases de efeito estufa (GEE) e no processo de descarbonização da economia será decisivo.
Neste artigo, colocaremos o foco nas instalações de hidrogênio verde e faremos uma breve análise, em virtude das características e das propriedades do hidrogênio, de como o conceito de segurança aplicável deve ir muito além do simples cumprimento de obrigações legais, de regulamentações industriais, do regulamento técnico ou de padrões de design. Para isso, será necessário o uso experimentado de ferramentas avançadas para identificar, avaliar e gerenciar os riscos, que servirão de suporte na administração e na tomada de decisões.
O objetivo de todos os agentes envolvidos na indústria associada ao hidrogênio verde (operadores, usuários, administração, seguradoras) é alcançar os mais altos níveis de segurança, tanto no design e na engenharia como na operação e manutenção, garantindo minimizar a ocorrência de acidentes nas instalações e, portanto, a continuidade das operações e do negócio.
A produção do hidrogênio e a estratégia da Comissão Europeia
Na atualidade, 95% do hidrogênio produzido na UE é principalmente obtido por reformado a vapor de metano com emissões de CO2 associadas (cerca de 330 g CO2eq/kWhH2)2. É o denominado hidrogênio cinza ou “derivado de fósseis”, na estratégia da Comissão Europeia3.
Este processo pode ser complementado com a coleta, utilização e armazenamento de CO2 para originar o hidrogênio azul, que pode ter uma pegada de carbono entre 70 e 90% inferior. A maior parte do 5% restante da produção atual é obtida como um coproduto da indústria do cloro-soda, que emprega eletrolisadores alcalinos.
A via eletrolítica se destina a experimentar um crescimento muito rápido em função das políticas comunitárias e nacionais. Mas para que o hidrogênio possa receber a qualificação de renovável (verde), a eletricidade deve ter esta característica, com a possibilidade de alcançar pegadas de carbono menores que 30 g CO2eq/kWhH2. Com certa dose de realismo, a Comissão identifica o “hidrogênio baixo em carbono” como aquele com pegada de carbono significativamente reduzida, seja produzido por reformado de metano com captura ou por eletricidade parcialmente renovável.
Hoje em dia, o hidrogênio é principalmente empregado em refinarias para eliminar a poluição e gerar produtos de qualidade em conformidade com a demanda (33%), fabricação de amoníaco (27%), metanol (11%) e produção de aço por redução direta de mineral de ferro (3%). Da produção de hidrogênio, 64% é on site, cativa, destinada a processos da própria fábrica.
O Green Deal da UE estabelece como objetivo reduzir as emissões de gases de efeito estufa (GEE) para 50% em 2030, tornando-se necessário um rápido processo de descarbonização da economia. Para isso, entre outras linhas de atuação, a Comissão Europeia publicou em julho deste ano a Estratégia da União Europeia para o Hidrogênio (COM (2020) 301 final), em que a produção de hidrogênio verde por eletrólise da água mediante eletricidade renovável conforma a tecnologia chave, que possibilitará a inserção no sistema energético de quantidades crescentes em diferentes formas conhecidas como Power-to-X.
Esta estratégia busca tornar o hidrogênio em parte intrínseca de um sistema energético integrado, que conte no ano 2030 com pelo menos 40 GW de eletrolisadores, produzindo 10 milhões de toneladas/anuais e em que o hidrogênio seja o pilar básico de um sistema energético descarbonizado e a matéria-prima para processos industriais, entre os quais tem destaque a fabricação de combustíveis sintéticos.
A Figura 1 reflete esta apreciação, em que os recursos para a obtenção do hidrogênio são diversos: de gás natural e biometano à eletricidade renovável. Evidentemente, a prioridade está em que seja renovável (verde) a maior parte do hidrogênio, obtido mediante eletrólise com eletricidade de origem eólica e solar, por ser a opção mais compatível com o objetivo de neutralidade climática para 2050.
Que propriedades do hidrogênio são mais relevantes em relação à segurança e outros combustíveis?
O hidrogênio é um gás incolor e inodoro, não tóxico e classificado como gás extremamente inflamável, de acordo com a regulamentação em vigor. De fato, para causar a ignição do hidrogênio é necessário 15 vezes menos energia que para o gás natural. E a faixa de concentrações no ar, em que o hidrogênio é inflamável, com chama invisível ao olho humano, é 10 vezes maior que para a gasolina.
Possui uma densidade muito baixa. É 14 vezes mais leve que o ar, 22 vezes mais leve que o propano (Figura 2) e propaga-se com muita rapidez. Em caso de vazamento, ele se elevará e dispersará rapidamente (mais de 20 m/s), ao contrário do que acontece, por exemplo, nos vazamentos de propano ou de outros combustíveis, que tendem a uma acumulação perto do solo por serem mais densos do que o ar. Em qualquer caso, é imprescindível abordar avaliações de riscos de explosão com a incorporação de medidas adequadas (equipamentos aptos para utilização em atmosferas classificadas, ventilação, etc.) para garantir a adequada prevenção de riscos de explosão.
A combustão do hidrogênio possui algumas especificidades relevantes.
- A temperatura de autoignição, a menor temperatura em que uma substância entra em ignição espontânea, sem necessidade de faísca ou chama, é muito semelhante à do gás natural e muito mais alta que a do vapor de gasolina (Figura 3). Isto representa uma vantagem do ponto de vista da segurança.
- Por outro lado, o hidrogênio apresenta um amplo nível de concentrações no ar em que pode acontecer a ignição (limite de inflamabilidade entre 4 e 75% em volume), muito maior do que outros combustíveis gasosos (Figura 4). No entanto, a concentração do hidrogênio a partir da qual a mistura é inflamável (limite inferior de inflamabilidade) é maior que a do propano e dos vapores de gasolina, que também representa um ponto a favor da perspectiva da segurança.
- A energia requerida, em condições de combustão ótimas, para iniciar a combustão é muito menor que para outros combustíveis, porque uma pequena faísca pode iniciar a combustão (Figura 5). Isto deve ser considerado ao reunir equipamentos de trabalho que possam atuar como fontes de ignição potenciais, embora a elevada velocidade de propagação possa jogar a nosso favor, conforme o caso.
- Finalmente, a combustão do hidrogênio origina uma chama invisível ao olho humano, motivo pelo qual são utilizados detectores de gás e chamas, e câmeras de visão térmica na sua identificação. A necessidade desses equipamentos é relevante, pois a radiação térmica originada não produz sensação de calor, por estar majoritariamente na faixa UV.
Estas propriedades analisadas fazem com que instalações industriais que geram, processam e armazenam hidrogênio tenham associado determinado nível de risco respeito de elementos vulneráveis (pessoas, meio ambiente e instalações ou ativos industriais), originado por eventos indesejados. Assim, é necessário contar com barreiras de segurança suficientes, bem com uma adequada gestão de riscos, visando evitá-los ou minimizar suas potenciais consequências.
A gestão da segurança na indústria do hidrogênio verde
O objetivo de todos os agentes envolvidos na indústria associada ao hidrogênio verde é alcançar os mais altos níveis de segurança: tanto no design e na engenharia, como na sua operação e manutenção, garantindo a minimização da ocorrência de acidentes nas instalações e, portanto, a continuidade da operação e do negócio.
Em função das características do hidrogênio acima mencionadas, o conceito de segurança aplicável deve ir muito além do simples cumprimento de obrigações legais, de regulamentações industriais, da regulamentação técnica ou de padrões de design. Além disso, é necessária a utilização experimentada de ferramentas avançadas para identificar, avaliar e gerenciar os riscos, como suporte para a administração e tomada de decisões.
Este critério é atualmente aplicado por operadores de instalações que produzem hidrogênio através de outras vias (especialmente, o denominado hidrogênio cinza por reformado a vapor de metano) em refino, indústria química e petroquímica. A entrada de novos atores de diferentes setores na produção de hidrogênio precisa, sem dúvida, replicar os elevados padrões de segurança implementados por essas atividades.
Com o objetivo de alcançar esses altos padrões de segurança, são brevemente apresentadas abaixo as principais ferramentas disponíveis, que podem ser aplicadas na gestão de riscos na indústria durante as diferentes etapas do ciclo de vida das instalações (Figura 6).
Além de serem práticas habituais na indústria, muitas delas são prescrições do setor segurador voltadas a minimizar que os riscos de um evento indesejado, a indisponibilidade ou a inatividade no processo originem danos ou perdas de produção.
Segurança no design
Na etapa de design e engenharia (conceitual, básica e de detalhe), as plantas devem ser concebidas com segurança intrínseca, para reduzir ao mínimo o risco tanto no interior quanto no exterior. Nesta fase, é chave realizar uma análise de riscos exaustiva e aplicar técnicas adequadas para gerenciar todas as possíveis situações de perigo.
São incontáveis as diferentes ferramentas (HAZID, HAZOP, Análise SIL, LOPA, FMECA, QRA, BRA, FERA, FIRE&GAS, ALARP, BOW-TIE, ATEX, Human Factors Engineering, Análise de Riscos por Fator Humano (Human HAZOP, SCTA), etc.) que podem ser utilizadas de acordo com a fase de engenharia em que nos encontramos, do projeto a ser desenvolvido, do objetivo buscado e da política de gestão de riscos que o promotor do projeto e a engenharia definiram como válidas para alcançar esses objetivos. Sua aplicação permite, durante todo o ciclo de vida de uma instalação industrial, obter importantes benefícios em segurança, como:
- Identificar situações de perigo de origem interna ou externa, que possam ocasionar um cenário de acidente em que esteja envolvido o hidrogênio ou outras substâncias presentes, ou em algumas das operações em fase de construção e exploração da planta, incluindo aquelas originadas pelo Fator Humano.
- Avaliar os danos causados por potenciais acidentes, quantificando os efeitos e as consequências em elementos vulneráveis (pessoas, meio ambiente e bens)
- Determinar as probabilidades de ocorrência de acontecimentos iniciadores de uma situação de perigo e suas diferentes evoluções potenciais.
- Quantificar e avaliar os riscos.
- Identificar barreiras de segurança preventivas e mitigadoras a serem implementadas para controlar os riscos até níveis aceitáveis.
Somente para citar alguns exemplos práticos de aplicação de algumas dessas ferramentas na fase de design ou de boas práticas recomendadas pelas companhias de seguros, e considerando as propriedades do hidrogênio acima mencionadas, encontramos as seguintes análises:
- Análise SIL, que permite projetar e implantar o ciclo de vida dos Sistemas Instrumentados de Segurança (sistema de encravamentos de emergência ou interlocks), de acordo ao regulamento de boas práticas sobre Segurança Funcional, para o correto design, operação e manutenção desses sistemas com critérios de segurança e confiabilidade.
- Fire&Gas, orientadas ao correto design e localização dos detectores de chama e hidrogênio como barreira de segurança, para identificar potenciais eventos perigosos em fases precoces, ativar mecanismos de resposta necessários e mitigar possíveis consequências. Os estudos Fire&Gas permitem localizar de maneira otimizada os diferentes tipos de sensores, sendo muito importante o design do tratamento dos sinais de medição e sua transmissão, para uma rápida e eficaz ativação dos protocolos.
- FERA (Fire and Explosion Risk Assessment), definir a mais adequada e ótima implantação e localização de equipamentos de processamento e, especialmente, de seus equipamentos críticos, em função das consequências e dos riscos analisados, determinando também suas necessidades construtivas para suportar os efeitos adversos.
- BRA (Building Risk Assessment), com a finalidade de definir a melhor localização de prédios e salas de controle, bem como dos parâmetros de design estrutural, para garantir sua integridade em caso de serem afetados por valores de sobrepressão e/ou radiação térmica que requeiram um nível de proteção especial para as pessoas e os sistemas de controle das instalações no interior.
- Estudos ATEX: Classificação de Áreas perigosas, Avaliações de Riscos de Explosão e Documento de Proteção Contra Explosões, em cumprimento das obrigações impostas pelo RD 681/03. A realização deste tipo de estudos deve levar em consideração as condições específicas de cada instalação, avaliando pormenorizadamente cada potencial fonte de ignição, uma a uma, em cada área classificada. Como boas práticas, a implantação de etiquetas NFC incluindo a informação relevante do equipamento começa a estender-se, também em matéria ATEX, facilitando a gestão da prevenção de riscos de explosão motivados por equipamentos elétricos e mecânicos. Além disso, é preciso prever a atualização periódica e por deterioração ou substituição desses equipamentos. E, por último, a avaliação novamente deve considerar o papel potencial do fator humano como origem de fontes de ignição.
- Human Factors Engineering, com a finalidade de verificar se o design das novas instalações: a) cumpre com os padrões em matéria de prevenção; b) responde a critérios ergonômicos; c) garante a acessibilidade de elementos críticos em situações de emergência; d) minimiza riscos de acidente potencialmente ocasionados pelo Fator Humano; e d) maximiza a operabilidade das instalações. Empreender este tipo de análise na fase de design (conceitual, básica e/ou de detalhe), elimina o custo de implantar medidas de correção quando as instalações já foram construídas e entregues. O HFE pode ser realizado com a integração de especialistas HFE nas equipes de design, ou mediante revisão de modelos 3D dos projetos à distância, à medida que são gerados nas diferentes fases de desenvolvimento da engenharia de projeto ou através de sessões HFE, similares às sessões HAZOP.
Segurança na operação
A operação exige a implementação de sistemas de gestão de segurança de processos que garantam o funcionamento adequado dos ativos. Esses sistemas tomam por base dois pilares fundamentais: o compromisso da organização com a segurança e o conhecimento e a gestão de riscos.
A prática habitual nos setores Oil&Gas e energético é adotar e implementar padrões de Sistema de Gestão de Segurança de Processos (PSM), com o objetivo principal de evitar a materialização de acidentes nas instalações onde são utilizadas, armazenadas, produzidas e/ou manipuladas substâncias com características perigosas, como o caso do hidrogênio.
PSM está fundamentado no desenvolvimento e na implementação dos seguintes pilares fundamentais de segurança:
- Alcançar um compromisso e liderança organizacional e pessoal inquebrantável com a segurança dos processos e das operações.
- Entender os riscos e perigos derivados dos processos químicos para sua identificação e avaliação.
- Gerenciar o risco contando com ferramentas que possibilitem seu monitoramento, acompanhamento, alarme, bem como barreiras de segurança disponíveis e confiáveis.
- Aprender da experiência, incorporando as lições assimiladas na revisão e melhoria.
A implantação de PSM abordará, no ciclo de vida das instalações (Figura 7), aqueles aspectos e questões fundamentais relacionadas à segurança, como:
- Design, engenharia e construção seguros
- Avaliação de perigos
- Alarmes eficientes
- Controle efetivo do processo
- Procedimentos adequados de entrada em operação e funcionamento das instalações
- Gestão das modificações
- Inspeção, teste e manutenção de equipamentos
- Formação do pessoal
- Relacionamento com provedores e fornecedores.
- Comunicações na organização e com seus gestores
Análise de riscos por fator humano
A análise de acidentes industriais tristemente célebres apresenta uma clara lição: a maioria deles atribui um papel chave às causas associadas ao erro humano.
Apesar disso, e paradoxalmente, o denominado Fator Humano não teve o papel relevante que lhe corresponde nas análises de riscos até pouco tempo. O surgimento de metodologias de Análise de Riscos por Fator Humano, como a análise de tarefas críticas (SCTA), o Human HAZOP ou outras aproximações sistemáticas, chegaram para atenuar em certo modo este déficit. Com este tipo de ferramentas, a aparente multiplicidade de desvios que o ser humano pode introduzir nos sistemas é parametrizada e a análise de riscos completada, de maneira a serem adotadas medidas de correção e controle (conforme apresentado no exemplo da Figura 8) que minimizem a probabilidade de ocorrência de comportamentos anômalos (erros, distrações, lapso ou violações) e, especialmente, que levem a reduzir a transcendência ou as consequências desses comportamentos anômalos.
Para isso, é imprescindível conhecer os condicionantes reais que podem originar as falhas na operação das instalações (PIF, Performance Influencing Factors, em sua versão anglo-saxã). As Análises de Riscos por Fator Humano analisam de maneira sistemática os desvios que os operadores podem introduzir nos sistemas, considerando os PIF, avaliando as consequências esperáveis (acidentais ou não), levando em conta as salvaguardas disponíveis e definindo as medidas de correção e controle que é preciso introduzir. Estas medidas de correção a serem introduzidas, que são o verdadeiro motivo para realizar estas análises, podem abranger a implantação de elementos de segurança de processos, indicadores, relocalização de equipamentos ou comandos, etc., e não apenas medidas de formação e informação, ou de caráter organizacional.
Confiabilidade e manutenção
A integridade de um ativo físico representa a sua capacidade para desempenhar suas funções de forma eficaz e eficiente, contribuindo para o cumprimento de objetivos individuais, coletivos e de grupos de interesse, ao mesmo tempo que seu estado e conservação são preservados, respeitando em todo momento a segurança e o meio ambiente.
Este enfoque do comportamento operacional de determinado equipamento, sistema ou instalação é fundamentado na gestão integrada dos seguintes aspectos durante a fase de exploração dos ativos em uma planta de hidrogênio:
- Desempenho do ativo físico ou nível de eficácia alcançado por um ativo em termos de Disponibilidade (capacidade para atender à demanda de funcionamento do ativo físico), Confiabilidade (capacidade do ativo de não deixar de cumprir suas funções) e Manutenção (capacidade de conservar e recuperar a funcionalidade do ativo físico perante processos de degradação ou avarias).
- Risco associado à exploração do ativo físico, entendido como o dano que pode ser gerado em certo intervalo de tempo em decorrência da aparição de avarias. Deve ser gerenciado de maneira apropriada, sob um enfoque proativo, priorizando as perspectivas preventivas perante os comportamentos reativos e minimizando os impactos negativos que possem derivar dessas falhas.
- Custo incorrido, que permita obter um lucro sustentável no tempo, gerando permanentemente receitas que superem os custos atrelados ao desenvolvimento das atividades empresariais
A integridade dos ativos (Asset Integrity) requer a adoção de estratégias otimizadas de manutenção e confiabilidade dos equipamentos, infraestruturas e barreiras de segurança, com ferramentas semelhantes as estabelecidas pela norma ISO 55000 na otimização das instalações.
Cada instalação e ambiente operacional exige um processo de análise para definir as atividades, as técnicas, as ferramentas e a sequência de implantação mais adequadas em cada caso (Figura 9), considerando sua realidade operacional, os objetivos, os interesses, as capacidades e os recursos, o grau de maturidade da organização e o prazo disponível.
Por exemplo, são de grande utilidade e frequentemente utilizadas nos setores industriais Oil&Gas e Energético, e recomendadas pelas companhias de seguros as seguintes entre outras:
- Estudos de RAM (Reliability, Availability and Maintainability), para quantificar a probabilidade de potenciais falhas de equipamentos, estimando a disponibilidade da planta de geração de hidrogênio e focando as ações de manutenção com uma ótima relação custo/benefício.
- Estudos de RCM (Reliability Centered Maintenance), que persegue a ótima alocação dos recursos disponíveis para a manutenção de uma instalação, focando nos ativos mais críticos para a funcionalidade da instalação e, portanto, para a continuidade do negócio. RCM determina o tipo e nível de manutenção que devem ser aplicados nos equipamentos em função do risco associado a suas falhas potenciais.
- Estudos de RBI (Risk Based Inspection), para monitorar o estado e a evolução dos componentes estáticos na instalação, com base na realização de inspeções para verificar o estado mecânico e de integridade dos equipamentos em função do risco introduzido por cada elemento. Determina a série de inspeções e ensaios, com o objetivo de obter a maior quantidade possível de informações sobre a vida restante de elementos e equipamentos.
Uma adequada estratégia de integridade de ativos e a aplicação de suas ferramentas incrementará a confiabilidade e disponibilidade de uma planta de hidrogênio, minimizando riscos e garantindo o retorno do investimento realizado na implementação.
Planificação de emergências e continuidade do negócio
Assim mesmo, e não menos importante como aspecto chave para a barreira de segurança, é a necessária planificação para emergências e continuidade do negócio (Figura 10), que estabelecerá uma resposta organizada de todos os meios humanos e materiais limitando as consequências em caso de acidentes.
Quanto à organização e aos meios humanos, é chave estabelecer as operações do plano de emergência, bem como os procedimentos de atuação a seguir. Em relação a estes últimos, também é recomendada a prática no setor segurador da elaboração e implementação dos denominados Fire Pre Plan, para cada cenário de acidente que possa incluir o hidrogênio ou outras substâncias como oxigênio, assim como nos diferentes equipamentos de processos (eletrolisadores, compressores, armazenamentos, etc.). Nos Fire Pre Plan são detalhados, por exemplo: o plano pormenorizado da zona e alcance das consequências, meios, contra incêndios/emergências disponíveis e a empregar ou mobilizar, equipamentos quentes ou críticos próximos envolvidos, instruções de atuação do pessoal de operações e das equipes de emergência.
Ainda, elementos como os sistemas de detecção e as proteções passivas e ativas contra incêndios são aspectos fundamentais no design das instalações e de resposta à emergência. Nesse sentido, os operadores deverão considerar os riscos específicos do hidrogênio ao definir essas proteções e sistemas. A planificação baseada na melhoria contínua requer a formação teórica e prática do pessoal chave e a realização de exercícios e simulações.
E, por último, no plano de gestão e operatividade superior à própria gestão da crise e Planos de Emergência se encontram os Planos de Continuidade de Negócio, que permitirão identificar potenciais ameaças contra a operação da planta e estabelecer adequadas estratégias de continuidade, para garantir a resiliência das instalações de hidrogênio verde.
Conclusões
É possível observar e concluir que a aplicação de todas estas ferramentas para identificar, avaliar e gerenciar os riscos em instalações de hidrogênio verde permitem desenhar instalações intrinsecamente seguras, identificar e avaliar riscos (o risco zero não existe), garantir uma adequada gestão, minimizar a materialização de acidentes e estabelecer mecanismos de resposta para maior disponibilidade dos ativos, contribuindo para a continuidade do negócio.
Por iso, é extraordinariamente importante que promotores e operadores de projetos de hidrogênio verde atribuam um lugar preferencial à segurança e aos riscos em todo o ciclo de vida dos projetos, com o suporte de especialistas nos diferentes âmbitos descritos.
Neste sentido, cumprir os objetivos da Comissão e dos promotores de projetos dependerá, entre outros fatores, da criação de uma indústria do hidrogênio verde segura e confiável, em que a aparição de “showstoppers” seja minimizada por uma gestão solvente e experimentada, assim entendida pelas partes envolvidas.
Autores:
Gabriela Reyes Delgado. Chefe do Departamento de Segurança Industrial da INERCO.
Juan Santos Remesal. Diretor da Divisão de Segurança Industrial da INERCO.
Pablo. Navarro González. Diretor Gerente da INERCO Prevenção de Riscos.
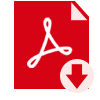