La descarbonización de los sectores estratégicos es objetivo prioritario de las grandes economías. Industrias como la aeronáutica se apoyan en la innovación para reducir sus emisiones. Hablamos de ello con Elena Rodríguez, Responsable de I+D+i en el Centro Tecnológico AIMEN.
¿Por qué descarbonizar el sector de la aviación es un reto tan complicado? ¿Cómo es el contexto en el que nos encontramos?
A medida que las economías y las poblaciones crecen, la demanda de bienes aumenta, al igual que el número de personas con el deseo y los medios para viajar. A nivel mundial, se espera que la actividad total del transporte se duplique con creces en 2050 en relación a 2015. Cualquier avance tecnológico en la descarbonización del sector de la aviación se vería simplemente compensado por el aumento de la demanda de movilidad.
La aviación representa actualmente el 2% de las emisiones mundiales de CO2 y el 3,8% de las emisiones en la Unión Europea, pero el crecimiento previsto del tráfico aéreo hará que las emisiones globales se tripliquen en 2050.
En un contexto de compromiso mundial para reducir drásticamente el impacto en el medio ambiente, la UE ha fijado objetivos ambiciosos (como la neutralidad climática para 2050) que han sido adoptados en la aviación, obligada a adoptar rápida y ampliamente una nueva generación de aeronaves con mejoras decisivas de rendimiento. Esto supone un reto complicado, ya que afecta a toda la cadena de valor de la fabricación de aviones, tanto en lo que se refiere al desarrollo de nuevas estructuras más ligeras (nuevos diseños y materiales) como de los sistemas de propulsión más sostenibles, sumado a la fuerte inercia de un sector en el que introducir cambios que afecten a sus procesos de certificación siempre es muy tedioso, conlleva muchos años de desarrollos, y, por lo tanto, resulta muy costoso. Proyectos de I+D como CAELESTIS contribuyen a introducir dichos cambios, basándonos en nuevos conceptos de diseño de componentes ligeros y nuevas maneras de fabricar desde la perspectiva digital.
Nos gustaría hablar en concreto de este proyecto europeo, CAELESTIS, en el que participa AIMEN. ¿Cómo se dan los primeros pasos?
La idea parte de la necesidad de garantizar una digitalización integral de la cadena de valor de la industria europea que permita la optimización de los procesos de fabricación y la aceleración de certificación de nuestras estructuras aeronáuticas, exigidas por los nuevos compromisos en materia de sostenibilidad y electrificación.
En este sentido, CAELESTIS, proyecto liderado por AIMEN, conectará los softwares de diseño, simulación e ingeniería distribuidos a lo largo de la cadena de valor para agilizar los procesos de intercambio de información y explotar las capacidades de superordenadores en los ciclos de optimización basados en simulación. Todo ello se valida en un caso de estudio concreto en el que se busca también demostrar el aligeramiento de las aeroestructuras y su fabricación optimizada disminuyendo el número de pasos durante la fabricación con procesos automatizados y avanzados. Así, se desarrollará un nuevo concepto de OGV (outlet-guide vane, álabe director de salida), componente del motor que será multimaterial, aligerado, combinando procesos de fabricación aditiva con procesado de composite fuera de autoclave.
¿Cuáles son los objetivos principales de este proyecto?
El objetivo fundamental es permitir a la industria aeronáutica de la Unión Europea diseñar y fabricar motores y estructuras de aeronaves disruptivas con capacidades de predicción mejoradas para ampliar el espacio de diseño y reducir las incertidumbres potencialmente encontradas a lo largo del ciclo de vida del producto y de la ingeniería, que actualmente limitan su puesta en servicio.
Háblenos de los distintos participantes del plan y de cuál es la hoja de ruta que se han marcado.
El proyecto, que comenzó en mayo de 2022 y tiene una duración total de 42 meses, está formado por 11 socios ubicados en 8 países de Europa, empresas, centros y universidades cuya experiencia se divide en:
- Modelización y simulación del rendimiento mecánico y de procesos de fabricación.
- Sistemas de interoperabilidad, computación de alto rendimiento, Inteligencia Artificial y ciberseguridad.
- Sistemas de fabricación inteligentes y adaptativos para componentes compuestos y multimateriales.
- Difusión, comunicación, explotación, gestión de la propiedad intelectual y los datos.
- Fabricación de motores de avión.
¿Cuáles son los principales desafíos a los que se enfrentan o han ido afrontando?
La iniciativa se encuentra en su primera fase, en la que principalmente se han definido los requerimientos del proyecto que buscarán mejorar y acortar el proceso de llegada al mercado de las piezas de la industria aeronáutica. Este reto se intenta solucionar basándose en la digitalización y los prototipos virtuales.
Para esto, se desarrollará un Ecosistema de Simulación Interoperable (ISE por sus siglas en inglés) que permitirá el flujo de datos bidireccional entre las diferentes etapas del diseño y la fabricación de piezas aeroespaciales, con el objetivo de acelerar la fase de diseño y optimizar la producción, a la vez que se asegura la fabricabilidad de las piezas y se optimiza el diseño.
Este sistema interoperable contará con los siguientes desarrollos:
- Un hilo digital que conectará las fases de diseño, simulación y fabricación de las piezas aeroespaciales, estableciendo entre ellas un flujo de datos bidireccional.
- Gemelos digitales basados en modelos del diseño y la fabricación de las piezas que tendrán en cuenta y gestionarán la incertidumbre proveniente de los procesos de fabricación.
- Sistemas de computación de altas prestaciones (HPC) donde se ejecutarán las simulaciones del proceso de fabricación y comportamiento de la pieza.
- Sistemas de fabricación inteligentes de monitorización y control de los procesos que buscarán analizar y reducir el impacto de los defectos en el comportamiento en servicio de la pieza.
¿Podría decirnos en qué momento se encuentra la investigación y cuáles son los avances que se han logrado?
Por el momento se han definido los requerimientos de los desarrollos y demostradores del proyecto, y se ha hecho un diseño preliminar de los demostradores y de la arquitectura de los sistemas de simulación. Además, se harán desarrollos para extraer los datos de fabricación e implementarlos en los distintos modelos de simulación.
El objetivo es que entre los modelos se produzca una comunicación, definida en la arquitectura del sistema de simulación y que los resultados finales se validen comparándolos con los resultados reales obtenidos en la fabricación.
Actualmente, se está trabajando para conseguir un primer flujo de datos virtuales entre los modelos de simulación, y en empezar a generar datos reales con la fabricación de probetas.
Por otro lado, se está preparando el nuevo diseño del OGV para aligerar la versión actual, proponiendo nuevos materiales compuestos, introduciendo la fabricación aditiva y evolucionando los procesos automatizados y avanzados para fabricar la estructura multimaterial (composite-metal).
¿Qué expectativas tienen de cara a este próximo año?
El proyecto avanzará hasta utilizar los datos reales de la fabricación en el sistema de simulación y validar las soluciones de simulación con los resultados reales. Todo esto estará apoyado con sistemas de computación de altas prestaciones (HPC) para ejecutar las simulaciones, y con algoritmos de inteligencia artificial para crear datos sintéticos que enriquezcan las simulaciones y proponer soluciones de diseño alternativas y optimizadas.
En el próximo año se espera llegar a conseguir este flujo de datos reales obtenidos en la fabricación dentro del sistema de simulación. En los siguientes meses de proyecto se optimizarán las simulaciones hasta que sean validadas usando los datos reales de procesos y ensayos.
Si hablamos de la reducción de emisiones en el sector, ¿qué perspectivas diría que hay en este momento y qué agentes son los más importantes en su éxito?
Para el 2035, tres prometedores tipos de aviones de propulsión alternativa podrían ofrecer opciones viables a los aviones convencionales que emiten carbono, mientras que los aviones totalmente eléctricos con baterías podrían permitir un vuelo completamente libre de emisiones en las distancias más cortas.
El hidrógeno, por su parte, podría utilizarse para electrificar las aeronaves con pilas de combustible en distancias medias, o mediante combustión directa. Esta última podría aplicarse a cualquier aeronave que recorra las distancias actuales.
Perfil de la entrevistada…
Elena Rodríguez Senín es responsable de Unidad de Negocio y Coordinadora de Materiales Avanzados en el Centro Tecnológico de AIMEN. Licenciada en Química en Santiago de Compostela (Galicia), entró en contacto con el mundo de la Ingeniería de Materiales en Madrid, donde se doctoró en la Universidad Carlos III en el año 2006.
Poco después, entró a formar parte de AIMEN, donde empezó como técnico junior y, donde en 2014, fue nombrada Coordinadora de la Unidad de Materiales Avanzados dentro del área I+D, cargo que ocupa en la actualidad.
Sigue leyendo… La sostenibilidad industrial comienza en el diseño
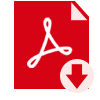