El término pellets —traducido al castellano como gránulos— se ha popularizado en las últimas semanas, tras el vertido en aguas portuguesas del mercante Tocanao, cuya carga extraviada incluía más de veintiséis toneladas de pellets de plástico que han inundado el mar y alcanzado costas españolas.
La industria plástica tiene relevancia internacional, ya que es insumo principal en una amplísima variedad de aplicaciones y, por tanto, en casi todas las actividades económicas. Según el último ‘Informe sectorial del plástico en España’, el sector del plástico en nuestro país está integrado por más de 3.700 empresas: una mayoría (3.374) se dedican a la transformación del plástico, además de los fabricantes de moldes, maquinaria y equipos para la fabricación (168). 162 empresas se dedicaban en 2023 al reciclado. Más de 125.000 personas están empleadas en el sector y el volumen de negocio equivale, según los últimos datos registrados, al 2,3% del PIB nacional.
La peletización de la industria
Los pellets (también conocidos como granzas, nibos o viveros, tal y como apunta la Comisión Europea) son pequeños gránulos —microplásticos de hasta 5 mm— que sirven de materia prima para producir todos los plásticos. Estas piezas, hoy en día, son imprescindibles para la industria ya que, gracias a su uniformidad y su pequeño tamaño, son más fáciles de manejar, transportar y transformar, tanto para la nueva producción como para el reciclado.
Los pellets suelen estar compuestos, principalmente, por uno o varios polímeros plásticos (como el polietileno (PE), el polipropileno (PP), el poliestireno (PS) y otros) y, en ocasiones, contienen otras sustancias aditivas. Cuando existe una mezcla concentrada de pigmentos o aditivos dentro del pellet se le conoce como masterbatch. Estas composiciones son utilizadas para producir desde productos electrónicos y automóviles hasta juguetes.
El proceso de fabricación de pellets de plástico conlleva, en esencia, cuatro pasos:
- la evaluación y gramaje de la materia prima (dosificación),
- el agregado de aditivos (mezclado),
- el corte y moldeado de las porciones escogidas (peletización)
- y la eliminación de agua contenida en el proceso (secado).
Para hacer esta transformación, en la actualidad existen tres maquinarias estándar, con un funcionamiento y objetivo diferentes:
- de filamentos —donde el corte se hace tras el enfriamiento—,
- de anillo de agua —da lugar a una granza redondeada y plana—
- y bajo el agua —que produce pellets esféricos—.
Compromiso para reducir el impacto ambiental
Situado en el centro de la polémica tras el reciente vertido que ha alcanzado cotas españolas, el plástico siempre ha sido objeto de críticas por su impacto ambiental. La peletización de la industria es, en este aspecto, un arma de doble filo para el sector. Por un lado, su fabricación consume menos energía y reduce las emisiones de gases de efecto invernadero, sus características hacen que sea más sencillo el procesado de plásticos usados para su reciclaje o reutilización, evitando residuos.
Por otro, las pérdidas de granza de plástico en el entorno son la tercera fuente de liberación no intencionada de microplásticos al planeta y estas se dan en todas las etapas de la cadena de suministro, desde la producción hasta el transporte y otras operaciones de logística y gestión de residuos. A este respecto, las principales instituciones internacionales participantes de la industria se ha mostrado comprometida con la rectificación de los riesgos derivados de la actividad. En abril de 2023, la Organización Marítima Internacional abordó, a través de su Subcomité de Prevención y Lucha contra la Contaminación, la clasificación de esta granza como carga peligrosa sujeta al Código Marítimo Internacional de Mercancías Peligrosas (IMDG), para aplicar a su transporte a regulación oportuna.
Por otro lado, en octubre del año pasado, la Comisión Europea publicó un informe con las medidas a adoptar con el fin de evitar la contaminación por microplásticos debida a la liberación involuntaria de los pellets. En dicho estudio, la Comisión Europea señala que pueden observarse cuatro tipos de efectos adversos ante los vertidos de pellets de plástico:
- En el medioambiente
- En el clima
- En la salud humana
- Y en la economía
Con esta propuesta, se pretende que los operadores que manipulan la granza en alguna de sus fases adopten una serie de medidas para que su impacto en los ecosistemas de su entorno disminuya entre un 54% y un 74%.
Medidas alineadas con un proyecto internacional
Las medidas propuestas por la Comisión Europea son compartidas por la iniciativa OCS (Operation Clean Sweep), un proyecto internacional de la industria de los plásticos que comparte el objetivo de reducir todo lo posible las fugas de granza y que cuenta con el apoyo y el compromiso de la Asociación Española de Industriales de Plástico (ANAIP). Las principales medidas a tomar, según esta organización, serían:
- Mejores prácticas de manipulación para los operadores económicos, que deben elaborar un plan de evaluación de riesgos para cada instalación y, así, optimizar su actividad y desarrollar medidas preventivas para evitar fugas.
- Certificación obligatoria en el caso de empresas que manipulen granza de plástico en cantidades superiores a 1.000 toneladas en el año civil. Dicho certificado deberá renovarse cada tres años para las grandes firmas y cada cuatro para las medianas.
- Las compañías de menor tamaño (microempresas y pequeñas empresas) harán frente a requisitos menos estrictos: deberán hacer autodeclaraciones de conformidad y declarar, a través de un sistema de notificación en los registros nacionales que crearán los estados miembros.
- Para facilitar la estimación de las pérdidas de granza, la Comisión Europea propone contar con una metodología estandarizada establecida en una norma armonizada adoptada de conformidad con el reglamento europeo, además de una mayor responsabilidad en línea con el incremento de la concienciación social respecto al impacto ambiental.
Este nuevo reglamento podría entrar en vigor a lo largo de 2024, aunque a día de hoy sigue sin contar con una hoja de ruta establecida para su asimilación en la industria.
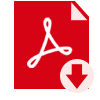