Basar el mantenimiento de una instalación en el diagnóstico previo de los equipos y sistemas que lo conforman, denominado genéricamente como mantenimiento basado en condición (MBC), es una estrategia de mantenimiento que ha proporcionado a muchas empresas dos de sus objetivos fundamentales en mantenimiento: reducción de costes y aumento de la disponibilidad de los equipos para la producción. Proporcionar estos resultados de una manera rápida supone para algunas empresas entrar en la senda de la viabilidad y de la competitividad, mientras que para otras significa obtener un beneficio mayor del que obtendrían basando el mantenimiento en otras estrategias como la simple corrección de averías o únicamente en las recomendaciones mínimas que proporciona el fabricante del equipo. Este artículo repasa las claves principales del MBC y sus ventajas frente a otras estrategias.
Los costes de mantenimiento de una instalación de tamaño medio o grande rondan entre el 2 y el 3% anual del coste total de la instalación. Eso significa que una empresa cuya reposición de activos está valorada en unos 100 millones de euros podría suponer entre dos y tres millones de euros al año incluyendo personal, contratos con las empresas externas y materiales. Este coste es, para muchas empresas, algo perfectamente asumible, pues supone muy poco en comparación con sus ingresos. Pero para otras le supone ‘pelear’ para ser más competitivas o incluso por su propia supervivencia, con lo cual se ven obligadas a reducir los costes. Una vía ‘brava’ de reducción es asignar un presupuesto pequeño a mantenimiento y que el propio departamento trate de gestionarlo como mejor pueda. Este tipo de soluciones, generadas de manera ciega desde el departamento financiero, no han dado un buen resultado pues lo único que consiguen es retrasar costes que en el futuro serán incluso más grandes que los que se pretenden ahorrar a corto plazo. Hay que recordar que lo que se haga hoy en la gestión del mantenimiento de una instalación ofrece sus resultados al menos seis meses más tarde.
No obstante, hay formas más inteligentes y eficaces para producir el mismo efecto, es decir, reducir los costes anuales de mantenimiento sin sacrificar la vida útil y sin incrementar los costes en el futuro. Una de estas opciones es basar el mantenimiento en el análisis previo de los equipos. Un mantenimiento basado en condición reduce costes hasta importes que oscilan entre el 1 y el 1,5 del coste de la instalación, sin comprometer la disponibilidad., la producción o aumentar la posibilidad de sufrir un siniestro. De hecho, la disponibilidad y la producción normalmente aumentan y la siniestralidad disminuye.
Para entender bien qué es esto y cuáles son sus consecuencias es necesario repasar ligeramente las otras opciones de las que se dispone. La primera de ellas, empleada por muchas empresas y que da en general resultados poco satisfactorios tanto en términos de coste como en términos de disponibilidad e incluso desde el punto de vista de la siniestralidad, es basar el mantenimiento en la solución de averías que se van produciendo.
Un mantenimiento basado en condición reduce costes hasta importes que oscilan entre el 1 y el 1,5 del coste de la instalación, sin comprometer la disponibilidad., la producción o aumentar la posibilidad de sufrir un siniestro.
Mantenimiento basado en la solución de averías
Es una estrategia puramente reactiva en la que simplemente se espera que las diversas máquinas que compone la instalación tengan un fallo y entonces se actúa para corregirlo. De este modo la producción pierde fiabilidad e incluso el coste es incierto, siendo muy variable de un año a otro ya que depende de las averías que se puedan producir. Por supuesto, cuando se produce la avería suele ser mucho más grave que la que se habría producido si los síntomas se hubieran detectado mucho antes.
Mantenimiento basado en la vida útil de los equipos
Junto con esta estrategia correctiva existe la posibilidad de basar el mantenimiento exclusivamente en las recomendaciones de los fabricantes. Estas recomendaciones suelen orientar el mantenimiento hacia una estrategia sistemática, es decir, la realización de una serie de tareas por horas de funcionamiento o por periodos de tiempo naturales y que implican en muchos casos la sustitución de determinados componentes por haber alcanzado dichos componentes el final de su vida útil. Así se estima que un rodamiento dura ‘X’ miles de horas, que un filtro hay que cambiarlo cada cierto periodo de tiempo o que hay que desmontar y sustituir piezas internas de determinados componentes de gran calado (turbinas de vapor y gas, motores alternativos, bombas, compresores, etc.) porque han alcanzado un número determinado de horas de operación o porque se establece que cada cierto tiempo hay que someter al equipo de instalación a una gran intervención.
Con el MBC se reduce el número de paradas provocadas por averías producidas
Mantenimiento basado en condición (MBC)
La estrategia de mantenimiento basado en condición o MBC huye de los planteamientos de sustitución sistemática de elementos por alcanzar el final de su vida útil estimada a priori por el fabricante. MBC plantea en cambio que deben intervenirse los equipos solo si existe algún síntoma de degradación. En el siglo XXI existen muchas técnicas para poder evaluar si un equipo se ha degradado y la mayoría de ellas son técnicas no invasivas, es decir, difícilmente pueden provocar daños por el hecho de realizarse. Además permiten determinar si los componentes de los equipos han agotado realmente su vida útil o no. Esto permite minimizar el número de intervenciones que se hacen en los equipos pues se realizan sólo en aquellos que realmente lo necesitan, cuando están dando algún síntoma de degradación en una fase temprana.
Técnicas de diagnóstico
Se suele asociar MBC a lo que se ha denominado durante mucho tiempo ‘mantenimiento predictivo’, es decir, a toda una serie de técnicas que tratan de establecer una relación entre determinadas variables físicas y la degradación que presenta una máquina, todo ello medido con equipos de cierto valor y complejidad. Aunque es cierto que este tipo de técnicas (análisis de vibraciones, termografías, inspecciones boroscópicas, análisis de aceite, análisis por ultrasonido, etc.) resultan muy útiles y casi imprescindibles en un MBC, ni de lejos son las más importantes ni las que más incidencias descubren en una instalación.
Puede establecerse que las técnicas de diagnóstico en las que se basa MBC se agrupan en cuatro categorías:
- RONDAS DE OPERACIÓN: Las rondas de operación son una serie de actividades, generalmente de inspección, que realizan los operadores de la planta. Consisten básicamente en inspecciones sensoriales y pruebas de funcionamiento. La frecuencia es elevada y puede llegar a realizarse una vez de forma diaria o incluso cada pocas horas. Los operadores descubren casi el 40% de los problemas en una fase temprana ya que muchos de los problemas que tienen las máquinas son detectables a simple vista.
EL MBC permite mantener la buena condición de uso mucho más allá de la vida útil que suelen establecerse en general para los equipos industriales
2. INSPECCIONES SENSORIALES DETALLADAS. Las inspecciones sensoriales detalladas son inspecciones llevadas a cabo por especialistas en mantenimiento (mecánicos, eléctricos e instrumentistas) con fuertes conocimientos en dicha materia. Aunque fundamentalmente se trata de pruebas de funcionamiento e inspecciones sensoriales, a veces implican paradas de máquinas o determinados desmontajes. Incluyen generalmente todas las tareas de las rutas de operación más otras tareas que no pueden ser llevadas a cabo por operadores. La frecuencia de cada una de las tareas es variable aunque hay una frecuencia que se repite muy a menudo en este tipo de inspecciones, esta es la frecuencia trimestral. Esto es debido a que muchas de las averías que se generan en una instalación tienen un periodo de incubación superior a tres meses, de manera que con inspecciones de carácter trimestral, es posible determinar el comienzo de gestación de determinados problemas.
3. MEDICIONES CON EQUIPOS OFF-LINE. El análisis con equipos de medición off-line trata de establecer una relación entre determinadas variables físicas (la vibración, la temperatura superficial, la generación de un determinado sonido, etc.) con el estado de degradación que presenta la máquina. Tradicionalmente se han llamado técnicas de mantenimiento predictivo aunque en realidad el concepto ‘mantenimiento predictivo’ no existe como tal, pues, la aplicación de estas técnicas ni permite predecir con exactitud cuándo se va a generar una avería ni es realmente mantenimiento ya que no compensa la degradación que el tiempo y el uso provoquen en los materiales. Estas técnicas cuya frecuencia en muchos casos también es trimestral, se refieren a los análisis de vibraciones, a termografías, inspecciones boroscópicas, análisis por ultrasonidos, etc. y tienen la característica común que el técnico que va a realizarlas lleva consigo los equipos, seguidamente los monta, obtiene las mediciones y saca sus conclusiones a partir de estas observaciones.
4. ANÁLISIS DE DATOS ONLINE. Hoy en día los equipos están muy monitorizados e instrumentados y además tienen sensores para captar online muchos parámetros de funcionamiento. A partir de la lectura de estos parámetros de funcionamiento y teniendo en cuenta que hay variables que deben estar fijadas en un rango estático y otras fijadas en rangos dinámicos, puede establecerse si un equipo está funcionado correctamente o no.
Las ventajas frente a otras estrategias
Como se ha detallado en este artículo el mantenimiento basado en condición puede aportar grandes ventajas al mantenimiento de la mayor parte de las instalaciones que conocemos. Estas ventajas están relacionadas principalmente con la disminución de los costes ya que si en una estrategia sistemática los costes no suelen bajar del 2% o 3% del coste total de la instalación, para un mantenimiento basado en condición es muy normal obtener ratios de entre el 1 y 1.5% del coste total de la instalación incluyendo personal, materiales y contratos de servicios con otras empresas.
La segunda de las grandes ventajas se refiere a la disponibilidad ya que el número de paradas para mantenimiento sistemático se reduce drásticamente. Adicionalmente, se reduce el número de paradas provocadas por averías producidas por la realización de una inspección no necesaria: cada vez que se abre un equipo se pone el riesgo el equipo, ya que pueden producirse averías que el equipo no tenía antes de abrirlos.
La tercera y última ventaja está relacionada con la vida útil de la instalación: un equipo bien monitorizado, del que se conoce su estado y en el que se interviene a tiempo una vez detectado el problema, mantiene su buena condición de uso mucho más allá de las vida útiles que suelen establecerse en general para los equipos industriales.
Perfil del autor
Santiago García Garrido
Director Técnico RENOVETEC
Santiago García Garrido es licenciado en ciencias químicas y doctorando en Ingeniería Naval. Ha sido director de la central térmica de ciclo combinado de San Roque, primera de este tipo puesta en marcha en España, y ha ocupado diversos cargos de responsabilidad en empresas como Duro Felguera o Gas Natural. En la actualidad es Director Técnico de RENOVETEC y Presidente de la Asociación Española de Ingeniería del Mantenimiento.
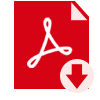