GABRIELA REYES DELGADO
Jefe Área de Seguridad de Procesos
PASTORA FERNÁNDEZ ZAMORA
Jefe Área de Análisis de Riesgos
ANTONIO DÍAZ PÉREZ
Jefe Área de Seguridad Industrial y Fiabilidad
ALFREDO RAMOS RODRÍGUEZ
Jefe Departamento Seguridad Industrial
JUAN SANTOS REMESAL
Director División Seguridad Industrial
Introducción y antecedentes
Los reglamentos industriales, la normativa técnica de referencia, los estándares de diseño y la experiencia acumulada son avales importantes para conseguir altos niveles de seguridad en el diseño e ingeniería de las grandes instalaciones industriales y, por tanto, asegurar la continuidad de la operación y del negocio.
No obstante, a pesar de cumplir con la normativa y códigos de diseño, el riesgo cero no existe y las instalaciones industriales diseñan e implementan medidas de seguridad para la gestión de sus activos con objeto tanto de reducir al máximo la probabilidad de ocurrencia de un incidente como de minimizar las consecuencias asociadas al mismo, siempre en consonancia con la seguridad de las personas, el medioambiente y las necesidades de producción y de rentabilidad de sus inversiones.
En la actualidad, la mayoría de las organizaciones que gestionan activos industriales implementan normas, estándares y procedimientos que van más allá de lo estrictamente legal y han superado las etapas tempranas en las que se asumía que los accidentes ocurrían o en la que se reaccionaba tras el suceso. En la actualidad la actitud proactiva para prevenir y evitar accidentes es la práctica habitual y para ello, los gestores de activos industriales deben asegurar la continuidad del negocio en todo su ciclo de vida utilizando herramientas dirigidas a conseguir la INTEGRIDAD en los siguientes tres vectores:
Integridad del diseño, aplicando herramientas de análisis de riesgo que permitan un diseño en el que los riesgos sean tan bajos como sea razonablemente práctico.
Integridad de la operación, implementando sistemas de gestión de seguridad de procesos que garanticen una operación segura de los activos y las barreras de seguridad.
Integridad de los activos, adoptando estrategias de manteniendo y fiabilidad optimizadas en los equipos, las infraestructuras y las barreras de seguridad.
Asset Integrity – Seguridad de procesos
El presente artículo propone profundizar en cada uno de los puntos anteriores relacionando las claves, las metodologías y las herramientas que los gestores de activos pueden aplicar para conseguir los objetivos empresariales de cada organización, así como la interrelación entre ellas como se indica en las figuras anexas. Todo ello pivotando sobre el concepto de SEGURIDAD en mayúsculas como soporte de la gestión y la toma de decisiones.
Asset Integrity – Seguridad de procesos
El diseño e ingeniería de procesos industriales basado en los reglamentos industriales, la normativa técnica de referencia, los estándares de diseño y la experiencia acumulada es uno de los elementos clave para conseguir altos niveles de seguridad.
En este sentido, las instalaciones deben diseñarse de forma que se reduzca al mínimo el riesgo tanto en el interior como en el exterior de las mismas, para lo cual es clave la realización un análisis exhaustivo y la aplicación de las herramientas adecuadas de análisis de riesgos en todas las fases del proyecto de cualesquiera sean las posibles situaciones generadoras de los mismos.
En cada sector se hace uso de criterios avanzados de seguridad, así como de estándares y normativas internacionales de aplicación. El conjunto de herramientas aplicadas en los proyectos van, entre otros, desde Estudios HAZID/HAZOP, Análisis SIL (Asignación del Índice SIL, Especificación de Requisitos de Seguridad o SRS y Verificación SIL), Análisis LOPA, Diseños de sistemas Fire&Gas, Quantitative Risk Analysis y ALARP, BOW-TIE, Determinación de Elementos Críticos de Seguridad y estándares de diseño para dichos Elementos. Estas herramientas de análisis de riesgos enfocadas a aumentar los niveles de seguridad y a lograr objetivos tales como:
Identificación de situaciones de peligro de origen exterior que puedan llegar a afectar al interior de la planta.
Identificación de situaciones de peligro de origen interno que puedan dar lugar a un escenario de accidente, tanto debido a las características de peligrosidad asociadas a las sustancias presentes, como a las operaciones en fase de construcción y explotación de la planta.
Estimación de las consecuencias. De acuerdo con las características de peligrosidad de las sustancias capaces de dar lugar a alguna de las situaciones de riesgo cuantificando los efectos y consecuencias.
Estimación de las probabilidades de ocurrencia de las situaciones de peligro identificadas, de forma que se pueda conocer el riesgo global de las instalaciones, una vez evaluadas las consecuencias de las mismas.
Identificación de aquellos puntos de las instalaciones en los que podrían requerirse mejoras en el diseño, inspecciones y mantenimiento de cara a una operación más segura.
Identificación de zonas, instalaciones, equipos y procesos que más contribuyen al riesgo, con objeto de establecer medidas de mitigación o protección adecuada para tener en todos los casos un riesgo asociado al establecimiento aceptable.
Definición de la estrategia de actuación en emergencia y la elaboración de planes de emergencia y contingencia.
Son innumerables las distintas herramientas que pueden ser utilizadas en función de la fase de la ingeniería en la que nos encontremos, el proyecto a desarrollar, el objetivo perseguido y la política de gestión de riesgos que el promotor del proyecto y la ingeniería hayan definido como válidas para alcanzar dichos objetivos. Su aplicación permite obtener importantes beneficios en seguridad durante todo el ciclo de vida de una instalación industrial.
A modo de referencia, la siguiente tabla trata de orientar para las distintas fases del proyecto, las herramientas de análisis de riesgos más adecuadas en función de los resultados esperados. Así mismo en la figura anexa se indica sus principales aplicaciones dentro de las etapas de ciclo de vida de la seguridad de una actividad.
FASE DEL PROYECTO | MÉTODO ANÁLISIS DE RIESGOS | RESULTADOS ESPERADOS |
---|---|---|
INGENIERÍA CONCEPTUAL | HAZID CHECKLIST WHAT IF | Orientación para la selección del proceso. Detectar peligros inaceptables de proceso. Ayuda para el diseño del proceso. Identificar modificaciones fundamentales en el proceso que reduzcan el nivel de riesgo. Ayuda a la localización geográfica del proyecto. |
INGENIERÍA BÁSICA | HAZID CHECKLIST WHAT IF FMEA HAZOP | Identificar con mayor detalle peligros en el proceso seleccionado y en el diseño propuesto; riesgos asociados a la localización geográfica; riesgos sobre equipos especiales o críticos en el proceso. |
INGENIERÍA DE DETALLE | CHECKLIST WHAT IF FMEA HAZOP SIL/VERIFICACIÓN Y SRS QRA FHA o EAC RAMS EERA SVA |
Identificar todas las situaciones de peligro en el proceso, valorando los riesgos asociados. Detectar aspectos de la operación no contemplados inicialmente. Ayudar a establecer los procedimientos de operación, comisionado y puesta en marcha. |
PLANTAS EN OPERACIÓN | CHECKLIST HAZOP SIL/VERIFICACIÓN Y SRS FHA o EAC QRA RAMS EERA SVA |
Garantizar la operación y que la información sobre calidad, requisitos legales, seguridad de proceso y procedimientos operativos es completa y esta actualizada. Incorporar las lecciones aprendidas en accidentes o incidentes recientes y valorar la incorporación de nuevos equipos, sistemas y tecnologías que mejoren los niveles de seguridad |
Diseño seguro e integridad técnica
Ciclo de Vida de la Seguridad – Herramientas y soluciones
Integridad de la operación. Sistema de gestión de seguridad de procesos (PSM)
Un Sistema de Gestión de Seguridad de Procesos, o PSM por su acrónimo en inglés, tiene como objetivo principal evitar la materialización de accidentes en aquellas instalaciones donde se utilicen, almacenen, produzcan y/o manipulen sustancias con características peligrosas y su consecución se soporta en dos pilares fundamentales como son el Compromiso de la Organización con la seguridad y el Conocimiento y Gestión de los riesgos asociados a los procesos.
La mayor parte de los sistemas de gestión se estructuran en torno al concepto de mejora continua, siguiendo los principios PDCA (Plan, Do, Check, Act). Los sistemas PSM no son ajenos a dichos principios. Por ejemplo, Energy Institute considera que un sistema PSM está formado por cuatro pilares, los cuales constan, a su vez, de veinte elementos básicos (Ver tabla adjunta).
PSM: ENERGY INSTITUTE
BLOQUE | ELEMENTOS |
---|---|
Liderazgo en Seguridad de Procesos | 1.Liderazgo, compromiso y responsabilidad. 2.Identificación y cumplimiento de la legislación vigente y de las normas de la industria. 3.Selección de personal, contratación y competencias y aseguramiento de seguridad y salud. 4.Participación del personal. 5.Comunicación con las partes interesadas. |
Identificación y Evaluación de Riesgos | 6. Identificación de peligros y evaluación de riesgos. 7. Documentación, registros y gestión del conocimiento. |
Gestión de Riesgos | 8. Manuales de operación y procedimientos. 9. Seguimiento de las variables operativas y relevos. 10. Gestión de interfaces operativas. 11. Normas y prácticas. 12. Gestión de cambios y gestión de proyectos 13. Disponibilidad de la operación y puesta en marcha de los procesos. 14. Preparación para emergencias. 15. Inspección y mantenimiento. 16. Gestión de los elementos críticos para la seguridad. 17. Control del trabajo, permisos de trabajo y gestión del riesgo de las tareas. 18. Contratistas y proveedores, selección y gestión. |
Revisión y Mejora | 19. Informes de Incidentes e investigación. 20. Auditoría, garantía, revisión de la gestión e intervención |
PSM – SEGURIDAD DE PROCESOS
GUÍA DE BUENAS PRÁCTICAS: ENERGY INSTITUTE
El PSM aborda en el ciclo de vida de las instalaciones los aspectos y cuestiones relacionadas con:
Diseño. ingeniería y construcción seguras.
Evaluación de peligros.
Alarmas eficientes
Control efectivo del proceso.
Procedimientos de puesta en marcha y operación de las instalaciones adecuados.
Gestión de las modificaciones.
Inspección, prueba y mantenimiento de equipos.
Formación del personal.
Relación con proveedores y suministradores.
Comunicaciones en la organización y en sus gestores.
Por ello, un adecuado diseño e implantación del PSM, en el que los aspectos anteriores se traten de forma integral, adaptada a la realidad de la organización y bajo el prisma de seguridad, permite:
Fomentar la cultura de la seguridad.
Identificar, evaluar y gestionar adecuadamente los riesgos de la instalación.
Identificar y gestionar los elementos críticos de seguridad de las instalaciones.
Establecer los procedimientos y medidas necesarias para el control de los procesos.
Garantizar la realización del mantenimiento e inspección de las instalaciones.
Disponer de profesionales adecuadamente formados y alineados con la seguridad de los procesos en todos los niveles y ámbitos de la organización.
Analizar y gestionar el impacto sobre la seguridad de los procesos de los cambios, tanto técnicos como organizativos.
Analizar y gestionar el impacto sobre la seguridad de los procesos de los cambios, tanto técnicos como organizativos.
Investigar las causas de los accidentes e incidentes y disponer las medidas para evitar que éstos se vuelvan a producir en el futuro.
Gestionar de manera sistemática y homogénea todos los aspectos que contribuyen al nivel de seguridad entre instalaciones o negocios del mismo Grupo.
Alcanzando entre otros los siguientes beneficios:
Mejora en la Gestión de los Activos y en los niveles de seguridad de las instalaciones.
Aumento de la disponibilidad de las instalaciones y de los niveles de producción.
Reducción de costes de reparación, lucro cesante y seguros.
Alineación de la organización hacia la consecución de los objetivos empresariales.
Aseguramiento del cumplimiento de obligaciones legislativas.
Reducción de la exposición a pérdidas financieras a gran escala, demandas, sanciones y reclamaciones de responsabilidad pública.
Mejora en la prima de seguros.
Mejora de la imagen corporativa de la compañía tanto interna como externa y otros beneficios intangibles.
Integridad de los activos. Asset Integrity
El concepto de ASSET INTEGRITY internacionalmente aplicado incluye aquellas prácticas, metodologías y técnicas de gestión de la integridad de activos dirigidas a optimizar el conjunto uso/riesgo/valor del mismo.
El uso de cualquier máquina, equipo o, en definitiva, activo industrial conlleva un cierto desgaste o degradación del mismo, pero, por otro lado, constituye la fuente (directa o indirecta) de creación de valor añadido (ingresos). Como consecuencia del uso se produce una cierta depreciación, asociada a que cada vez al activo le queda por delante una menor vida útil; pero la degradación del activo no tiene únicamente efectos económicos, también la seguridad, y por tanto los riesgos de la operación, así como la propia integridad del activo, se verán afectadas a lo largo del tiempo.
Uno de los medios a nivel industrial más utilizados para la gestión de la integridad de los activos es el mantenimiento industrial, en sus diferentes vertientes (preventivo, predictivo, correctivo…) pero además de estas técnicas “estáticas” se han desarrollado en los últimos años una serie de técnicas avanzadas para la optimización del conjunto Uso/Riesgo/Valor.
Todas estas técnicas pueden englobarse bajo una estrategia global de Gestión de la integridad de los Activos desarrollada en la norma ISO 55.000, dentro de la cual se desarrollan las técnicas para la optimización de la fiabilidad/disponibilidad/mantenibilidad de instalaciones industriales (RAM); para la optimización de la fiabilidad de máquinas y equipos dinámicos (RCM), o para la optimización de la integridad física de equipos (RBI).
Los requerimientos establecidos en las normas ISO 5500X proporcionan un enfoque estructurado para desarrollar un sistema de gestión de activos que facilite alcanzar el logro de los objetivos de la organización y proporcionando los controles necesarios para garantizar que así sea.
Esta norma ha venido a estructurar una necesidad en la industria motivada por la evolución en la madurez de las organizaciones y a entornos complejos y situaciones en las que el negocio se encuentra en entredicho por accidentes como el del Golfo de México (Macondo, BP) tal y como se muestra en la siguiente figura:
Adicionalmente, la gestión de las inversiones se realiza con un concepto de Ciclo de Vida en el que los costes operativos frente al riesgo o la fiabilidad adquieren una importancia capital. La comparación continua entre distintos escenarios de inversión se convierte en un ejercicio diario y fundamental para la toma de decisiones empresariales.
Conclusiones
Son innumerables las distintas herramientas que pueden ser utilizadas en función de la fase de la actividad en la que nos encontremos, el proyecto a desarrollar, el objetivo perseguido y la política de gestión de riesgos que la compañía haya establecido para alcanzar sus objetivos de seguridad.
La actitud proactiva para prevenir y evitar accidentes es la práctica habitual y para ello, los gestores de activos industriales deben asegurar la continuidad del negocio en todo su ciclo de vida utilizando herramientas dirigidas a conseguir la INTEGRIDAD en el diseño y operación, así como en la disponibilidad y fiabilidad de los activos.
La aplicación coordinada e integrada del conjunto de herramientas descritas en el presente artículo permite obtener importantes beneficios en seguridad durante todo el ciclo de vida de una instalación industrial, siendo para ello importante contar con la experiencia necesaria para elegir aquellas que se ajusten a la instalación a evaluar y a los objetivos perseguidos.
En este sentido INERCO cuenta con más de 30 años de experiencia asesorando en la gestión de riesgos y aumentando los niveles de seguridad integral en el sector industrial (Oil&gas, químico, energético, minería, metalúrgico, ingenierías industriales, etc.), utilizando los medios más efectivos en términos de costo-eficacia para la reducción del riesgo.
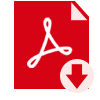