Cristina Leon Vera | 30/01/2025
The MAPFRE Global Risks Engineering assessment is characterized by its highly qualified professionals and the level of its recommendations and requirements consistent over time. It’s a demanding audit that the client really values. We at the MAPFRE Global Risks Engineering Area would like to publicize one of our functions: visiting the client and conducting the so-called Stress Test, an exercise designed to assess their ability to respond to emergencies. That’s why, through ‘Diary of an Engineer’, we want to help you understand what a typical inspection day is like: from hours of transatlantic travel and winding roads in a van or bus or whatver, in good weather and bad.
Monday, 8 October, 2024
It’s 7 o’clock in the morning and here we are at the train station. Today’s visit is local (in Spain) and the plan is to do a follow up on recommendations and a Stress Test. This type of work, called the MAPFRE Global Risks Engineering Assessment, is part of the suite of services we offer exclusively to our insured clients. Only professionals of the highest order are sent out to do these visits and make the highly regarded recommendations. Although the assessments are demanding, our clients really value these visits in that they can see firsthand that we’re not just looking out for the safety of their commercial activity, but that we’re also concerned for the well-being of their people and the integrity of their physical assets.
Today we’re going to visit a factory that manufactures wooden countertops and other products. We have to travel to the north of Spain so we still have a four-hour train ride ahead of us and two more hours on a coach due to roadworks. We spend this time time reviewing the intrinsic risks of the activity and the levels of protection reflected in the associated Inspection Report. We consider:
- Production processes: We must take into account the origin of the raw materials and the status, storage and processes performed on same (debarking, grinding, etc.)
- Pressing: The safety conditions of this process must be reviewed, highlighting the risk, the drying process, where thermal oil rollers and hydraulic units are used, as they are combustible and flammable products. We also review the existing safety, prevention and protection measures in place.
- Process line: Depending on the final product, a series of processes are carried out with specialized machinery such as the countertop shaper, stamping and so on. This factory also specializes in manufacturing floor coverings, where they deboss designs to simulate natural veins or other effects.
We’ll also have to review the facility’s ATEX areas (explosion risk areas, explosivity limits, certification of electrical equipment and voltage).
Finally, after more than six hours, we disembark to be received by the rain, which is nothing new in this area. The aroma of the eucalyptus hits us hard, as does a bracing freshness that’s absent from Madrid at this time of the year.
Wednesday, 9 October, 2024
We get up early to have breakfast and get to our appointment with the client and the broker, who also usually accompanies us on this type of visit. The storm hasn’t stopped all night and has brought total chaos to the city: traffic lights out of order, flooded and impassable streets. As you’d expect, taxis are scarce and getting one was an odyssey in itself. The adventures of being an Engineer Assessor continue…
Finally we reach our destination! The security personnel request our IDs so they can log our visit in the system before suggesting we watch a training video covering basic instructions related to navigating the factory so we don’t jeopardize our own personal safety or the safety of the facilities. When we finish watching the video, we answer a few questions about the safety information we’ve just received to show that we’ve understood everything correctly. Then we’re directed to the meeting room where we meet the Maintenance Supervisor, Workplace Accident Prevention Officer, Technical Managemnt, Legal Affairs Risk Management and the Account Executive from the broker. This meeting lasts almost two hours, mainly because it’s the time we have available to meticulously review the objectives, changes and recommendations, and go over the description of the solar-powered facility that the client has recently incorporated into their plant. It’s time to ask questions like: What changes have been made since the last visit? What protection measures are in place in the pressing stage? Is the solar panel installation for self-consumption or is the energy generated sold on to a third party? Is the cover made of a flammable sandwich composite material? Where is the boiler located? Are the forklifts electric or diesel? Do they have lithium batteries? What fire protection measures are in place? Are adequate wayfinding signs in place for firefighters? There’s no room for nagging doubts before the inspection, so now is the time to ask detailed questions to ensure everything matches up properly with the information previously received.
Finally, we put on the high visibility vests and we begin the guided tour of the factory (inside and outside), passing through the different areas that correspond to auxiliary facilities (transformers and plant rooms, boiler rooms, compressors, thermal oil circuit, etc.), the room housing the photovoltaic inverters, cyclones, the pressing line, etc.
In total, today’s workday lasted about 5 hours, and we’re exhausted by the high level of concentration and effort involved. Now it’s time to prepare for tomorrow, which is when we run the Stress Test.
Thursday, 10 October, 2024
The Emergency Plan Stress Test is a practical exercise that simulates an emergency situation that activates the protocol set out in the Self-Protection Plan. It’s not about doing things in record time, but it’s important that the emergency situation is resolved as soon as possible.
To this end, weeks earlier we’d held a meeting with the client in which we agreed on the scope and nature of the exercise. In other words, we decided on whether the emergency would be a fire or a spill, whether manual or automatic resources would be used, if there would be a partial or full evacution, etc. We even checked to see if they wanted to simulate the entry of emergency services. So we planned for the occurrence of a forklift fire outside in the area where the water tanks were located.
Before proceeding to the Stress Test, it’s essential that today we have the meeting with the different supervisors to review each of the phases and roles stipulated in the Self-Protection Plan drawn up by them: Head of Emergency and Response, Plan Manager, Emergency Coordinator, 1st and 2nd intervention teams and Control Center. All employees know what their role is and that today is the day in question.
In today’s exercise, the phases to be evaluated are very specific, as per the Self-Protection Plan inplace:
- Provoke a fire in the forklift
- Forklift operator gives the alert and the alarm goes off at the factory to report the incident
- Operators abandon activity and assemble at meeting points
- Fire extinguishing equipment is prepared
- Operator intervenes with the fire extinguisher
- The first intervention team deploys the hose
- The fire intensifies. Emergency services are called (firefighters/ambulance)
- Second intervention team uses the hose to spray water first and then foam
- The fire is not extinguished. The factory evacuation alarm sounds
- Each manager guides the operators in the charge to leave the warehouse using the safety lanes
- Emergency services arrive on site and extinguish the fire
In this type of exercise, it’s important to be very clear about everything in order to act as effectively as possible, given that the evaluation takes into account not only how the plan is executed and what role each function fulfills, but also the time taken to complete the exercise. We always advise clients that it’s advisable for the exercises to be carried out in a meticulous and disciplined manner, as opposed to quickly and with insufficient involvement, as this stress test is a perfect opportunity to put knowledge, rational behavior and coordination between emergency teams into practice as if it were a real situation.
Depending on what we observe during the visit, we generate two reports. First comes the plant audit itself and then there is the Stress Test assessment. These documents also include a series of requirements and recommendations that will be taken into account when renewing the policy and the next visit. These reports will be sent to the GEMA (Advanced Improvement Management) tool, where the client and insurance company can interact directly.
As engineers working for the insurance company, we must be aware that days like this are extremely nerve-wracking for the client. That’s why it’s important to convey a sense of empathy and peace of mind, while being professional and appreciating their collaboration. At the end of the day, this Stress Test involves a significant deployment of material and human resources.
It’s essential that the people responsible for enterprise risk management understand that having proper prevention and security measures in place saves the day when it comes to a real accident. And as an insurer, we must raise awareness, train and report on the risks they face and how to prevent them.
To wrap up, the expertize we offer in MAPFRE Global Risks and these exclusive services are invaluable for our clients and we must spread the word.
Article collaborators:
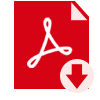