The creation of tunnels is a process with high technical complexity, both in terms of the type of machinery used and the medium through which it is performed. The builders’ main objective is to carry out the works avoiding damage to structures and services that are on the surface and also managing complex geological uncertainties.
The design and construction of a tunnel can present various obstacles. The first of them involves the type of terrain to be excavated, which can be soft (soil) or rocky (hard or medium-hard). The excavation method to be used, either with machinery or explosives, is chosen depending on the terrain’s characteristics.
In general, using tunnel boring machines leads to an improvement in safety compared to conventional tunnel excavation systems.
These machines drill the rock in full-bore, usually in a circular motion. Mechanical energy is produced by electric motors and transmitted to the rotating head of the device in the form of a rotating torque through hydraulic circuits.
This torque, together with the thrust provided by hydraulic cylinders to the head of the machine against the digging face, provides the mechanical energy to the cutting tools (the discs), which transmit it to the rock through the contact surface.
The level of energy released is capable of producing, first, penetration of the disc cutters and, second, fracture by traction and shearing of the rock between the series of concentric cutters mounted in the head of the device.
It is not always possible to use these machines. This is due to the type of material to be excavated, the length of the tunnel, and the availability and cost of the equipment.
However, despite these difficulties, using them continues to be one of the most beneficial methods of connecting two points with an underground road. These devices are generally the best option in terms of efficiency, reliability, execution time, cost, and safety.
Proper use
Each of the various tunnel boring machines has its advantages and disadvantages. To obtain the expected results, there must be careful planning even before choosing the equipment to use. Above all, a sufficient geological, geotechnical, and hydrogeological analysis must be conducted of the terrain to be excavated.
It is vitally important to be fully aware of the geological, geotechnical, and hydrogeological properties of the terrain in order to be able to design the most suitable excavation and support method.
It is also essential to take into account the services and infrastructure existing on the surface, both directly above the route line and in the surroundings. This is the only way to make the best decision regarding the type of tunnel boring machine to be selected, the corrective measures of the terrain, the pace of work, the safety measures, and the drilling intensity, among other aspects.
Safety as a guiding principle
Tunnel boring machines offer higher levels of safety compared to other excavation techniques. However, they do not eliminate all risks. Their use, while doing away with or reducing some of the hazards inherent to other techniques (such as explosives), does pose new challenges that must be fully known, understood, evaluated, and managed
Fundamentally, we can say that there are three types of risks: those that are due to the terrain’s geology, which can lead to accidents with very serious consequences as a result of ignorance of the terrain’s nature; risks inherent to the machinery and work facilities in the tunnel; and, finally, risks caused by the unique conditions of the work environment.
These risks are generally associated with handling large loads that can cause the machinery to collapse or overturn due to possible failures in the support terrain. Unsuitable foundations may also occur on tower cranes or bridge cranes.
In general, tunnel construction presents a number of risks that are caused by various factors, in particular the nature of the subsoil. It is vitally important to be fully aware of the geological, geotechnical, and hydrogeological properties of the terrain in order to be able to design the most suitable excavation and support method.
Tunnel excavation is the primary activity which also has the longest duration. In this work phase, it is important to differentiate between the different types of risks present.
Fundamentally, we can say that there are three types of risks: those that are due to the terrain’s geology, which can lead to accidents with very serious consequences as a result of ignorance of the terrain’s nature; risks inherent to the machinery and work facilities in the tunnel; and, finally, risks caused by the unique conditions of the work environment.
Special care must be taken when excavating the initial meters of the tunnel, as the tunnel boring machine must have sufficient support to be able to exert pressure against the face. Otherwise, there could be poor support in the gripper shoes due to unstable terrain. This could cause it to sink. Also the smallest lining could lead to collapses and detachments.
New times, new challenges
The new needs of society have led to the emergence of projects that are designed under parameters and carried out in geological conditions that would have been inconceivable a few years ago.
This requires the use of machines that are specially adapted to safely excavate underground infrastructure where necessary, regardless of the conditions in the subsoil.
But it also requires greater preparation and commitment from the operators responsible for turning projects into construction.
The truth is that, increasingly, tunnels must be built in heterogeneous geological areas. The combination of sections of solid rock with other sections of soft soils is common. Also, these variations may include faces with the presence of aquifers or with mixed conditions of rocks and soil or sandstone.
It is therefore much more demanding to design this machinery. They must be adequately prepared to dig and line the tunnel safely and reliably. In addition, they must do so without the need for long conversion times to adapt to specific soil conditions at each stage of the process. Only in this way will they be able to maintain levels of execution time and costs that make the work technically, operationally, and financially viable.
Cutting-edge technology faces a greater challenge
Alignments of tunnels with varying soil conditions have become a common challenge in many underground projects. Conditions throughout the tunnel often range from stable rock faces to soft soil with the presence of water. The standard technologies used by shield tunnel boring machines (TBMs) have been improved in order to be able to work in a wider range of terrain-specific conditions. However, there conditions is excessive variability in the terrain, technical and commercial limits are often reached.
This is why multimodal TBMs offer the option to modify tunnel excavation technology to adapt to the real conditions of the terrain and, therefore, to operate the TBMs in different modes.
Variable density tunnel boring machines are a new generation of multimodal machines for soft soils with state-of-the-art technology. Without major mechanical modifications, these machines combine the two basic technologies of enclosed soft ground tunnel boring machines, maintaining a permanent control of pressure on the face.
Variable density TBMs can be used as a classic slurry pressure tunnel boring machine using an air bubble system to control face pressure and in a earth balance pressure mode.
Modes can be changed between gradually with a permanent and complete control of the pressure of the tunnel face, and without the need for work in the chamber.
This machine can also operate using a high density in the excavation chamber, which would be too dense for classic slurry pressure operation, but too fluid for classic earth balance pressure operation.
Double shields are tunnel boring machines that have both mole and shield characteristics. It is a telescopic shield arranged in two pieces, designed to support the ground as it progresses through excavation of the tunnel. Its main feature is its double independent propulsion system, the first for the shield and the second for the mole.
The new needs of society have led to the emergence of projects that are designed under parameters and carried out in geological conditions that would have been inconceivable a few years ago.
It is a very versatile machine as it allows the hard rock that the shields themselves could not drill to be excavated, with yields similar to those of moles. But it can also be used in unstable and heterogeneous terrain where moles could not operate. It is therefore the best solution for rock masses with sections of variable soil-rock typology.
The machine has two shields: the front and the rear. The front supports the cutting head, contains the main bearing, the drive crown and the internal and external seals. The rear end, also called the anchorage shield, incorporates the keystone erector and thrust cylinders for normal shield mode propulsion.
These two parts move independently, in such a way that the head can dig while rings of segments accumulate on the end. The yields achieved are thus higher than with a single shield.
A world of benefits
Multimodal tunnel boring machine technology provides to opportunity to switch between various operating modes within the tunnel.
The large number of applications of this new generation of multimodal soft ground tunnel boring machines shows the advantage of having a safe solution even for potentially high risk areas.
Most current tunnel projects present a heterogeneous and complex geology and environment, with the additional requirement of passing under important and fragile structures.
With the latest variable density tunnel boring machine technology, these projects can be carried out safely and reliably.
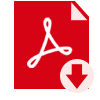