admin | 06/10/2020
The development of production processes is inescapably linked to management of the hazards they experience. That’s why industrial safety is part of any company’s value chain. The same emerging technologies that gave shape to Industry 4.0 have redefined the protection models that ensure risk mitigation and prevention in large companies.
The tech revolution that has transformed big industry has completely redefined the field of occupational and production safety. The use of measures to prevent and limit risks has found that emerging technologies are tools that can optimize the efficiency of traditional systems and create new techniques that fix the cracks in companies’ protection. Pedro García-Trejo, technical industrial engineer, explains some of the keys to us in these new circumstances in terms of industrial safety.
“I wouldn’t say that there is a gap between companies’ needs and the ability to resolve these problems. However, it is true that the requirements in the field of risk prevention are increasingly demanding. Optimizing production and achieving returns on investments means that, as tech experts, we must be able to present applications and products that resolve the security deficiencies in companies without decreasing or altering the existing standards of work,” the expert explained.
A new architecture
In order to successfully implement innovation in current safety systems, García-Trejo noted that technology integration must be pursued, avoiding the idea of a complete renovation. “In many cases, new technologies do not replace the current technologies in terms of the level of effectiveness, rather they complement them by improving the labor environment. For example, a camera that recognizes people should not be used to replace a laser scanner provided that the scanner is viable,” he asserted. Incorporating this set of technologies has brought a qualitative leap in occupational and industrial safety. In this field, problems can now be resolved that just a few years ago were impossible. And situations that previously were difficult to manage can become routine and easily handled. “For example, in the field of surveillance and supervision of lone workers, current technology allows us to locate an operator in areas without coverage. Some monitoring mechanisms currently used also offer the option to protect people who have to handle mobile machinery in factories or work areas, preventing accidents and minimizing possible impacts,” he stated.
The use of measures to prevent and limit risks has found that emerging technologies are tools that can optimize the efficiency of traditional systems and create new techniques that fix the cracks in companies’ protection.
In order to implement a new safety architecture in a company that is able to coordinate both current technologies and potential technologies, applied engineering works as a fundamental component in this plan. In this discipline, a combined structure is presented that analyzes both the existing deficiencies and the characteristics that can be provided by emerging technologies, without neglecting each sector’s specific needs and the priority for continuity in production. In this incorporation, which is being done worldwide quickly and unstoppably, fear of change must be avoided and the latest technology must be used to avoid vulnerabilities. Constant innovation in the technical and operational spheres are fundamental in this journey. “It is essential for there to be daily training, to be able to keep tech knowledge up to date. These days, the speed of change means that, if you stop for five minutes, you’ll miss something important, you’ll be out of touch, and therefore out of the market,” he insisted.
Lines of application
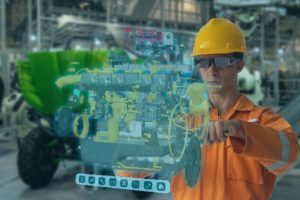
Sensor systems in industrial machinery are used to detect failures in mechanisms and prevent accidents caused by the wear and tear of their components.
Currently, there are now examples of successful implementation in safety systems of the same technologies that drive productivity in industries, which are applied both in operations and in the field of prevention and training.
- Virtual Reality: operators can use this to receive training in their work role without being exposed to the same risks resulting from inexperience and can even test their action and reaction during emergency scenarios.
- Sensor systems: Continuous monitoring of machinery prevents accidents caused by the wear and tear of their components, surveillance of property to ensure safe environments, and detect harmful agents and even monitor operators to protect them physically.
- Big Data and Artificial Intelligence: gathering and processing the immense volume of data produced by industrial operations leads to algorithms that can predict accidents and detect risks before they happen.
- Unmanned vehicles: drones are used on large construction sites to replace operators in carrying out high risk work, inspecting difficult-to-access areas, and performing work at significant heights.
- Exoskeletons: A type of armor or robotic support that is ergonomically adapted to workers, exoskeletons are used to avoid certain occupational risks, ensure the well-being of the wearers when performing repetitive or prolonged actions, and even improve the quality of the activity.
Progress in implementation
Safety systems quietly guarantee a company’s proper operation and, although they have no specific weight in the corporate image, they are themselves a return for the value chain. In addition to preventing risks that can jeopardize productivity or lead to economic losses, García-Trejo highlighted the negative effect an accident can have on workers. In this regard, there are certain sectors that are implementing emerging technologies with notable success. “Logistical areas like automated warehouses and cold storage warehouses, parts of big industry, are showing significant interest in protecting themselves from possible labor accidents. There is also a growing interest in managing the information this equipment collects, which is transferred to new cloud environments,” he added.
Controlling and monitoring these external storage services allows the level of surveillance to be widened and new work methods to be applied. “Data from safety sensors, such as vertical positions, incidents between moving machinery end-users, and many other variables, are recorded and stored on these platforms to later be processed and analyzed, which is used to create training plans and protocols” adapted to the specific needs of the areas impacted. To this end, the role of tech providers will be fundamental in this essential line of Industry 4.0. “The challenge is being familiar with and staying up to date and informed on the technologies we have available to us. In this regard, a good R&D department that is trained, experienced, and well coordinated is vital,” he concluded.
Article contributor:
Pedro García-Trejo is an industrial technical engineer with a degree from the University of Vigo, specializing in automation and electronics, and a Senior Technician in Labor Risk Prevention. He has a specialist certificate in explosive atmospheres from the Madariaga program at the University of Madrid.
In 1997, he founded GTG Ingenieros, an engineering company with over 20 years of experience in the field of industrial safety that worked with companies and groups in more than 16 countries. The company adapts technology to protect workers in industrial environments. Over these years, they have developed and patented several safety devices, and are pioneers in the use of radio frequency-based devices specifically designed for industrial safety and personal safety.
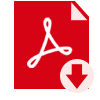