Current production processes entail a high number of participants and tasks that cannot be assessed individually, rather they require continuous monitoring and an overall view to ensure maximum effectiveness. The digital thread has arisen in this context to facilitate integration throughout the product lifecycle, from when it is just an idea to its removal from the market. It is so important that it is already having an impact on projects outside of the aerospace sector where it began and is being integrated into a number of Industry 4.0 sectors.
Massive worldwide digitalization is creating a new reality that companies must face, according to Carlos Gallego, Managing Director and Head of Industry X.0 at Accenture in Spain, Portugal, and Israel. The speed of innovation is greater than ever, the time between development cycles continues to decrease, and client expectations continually increase. “Only by making data-driven decisions can companies address client needs, provide new digital experiences, and increase operational efficiency,” he asserts.
In this context, companies must master the digital thread, which is the traceable dataflow that connects all the relevant systems and operating processes involved in the lifecycle of a product or service. In this way, a product or service can be adjusted, improved, and made more efficient throughout the entire process, from conceptualization to the end of its useful life. “In the field of operations, it is ultimately about getting the correct information from our factory or company, displaying it in a full virtual image, and then making sure that the right people see it at the right time, in real time,” says Gallego.
The digital thread is the traceable dataflow that connects all the relevant systems and operating processes involved in the life cycle of a product or service.”
In general, the digital thread covers four major product phases:
– Concept and design. A purely digital phase that uses data to subsequently produce the most effective prototype.
– Creation and monitoring. All the data from the previous phase are transferred to this engineering stage where the product is created for the first time.
– Testing, validation, and manufacturing. After confirming the functioning of the product or service, it moves to production. Depending on the digital thread, progress can be checked from the initial ideas to the final product.
– Product launch and delivery. Data are incorporated from the market or from the integration of the product into a larger process.
Opportunities for improvement
Data are an excellent source of opportunity if they are used and leveraged effectively. “The digital thread is becoming increasingly important tool for companies to efficiently and proactively gather information based on the data that enable them to improve product quality, increase process efficiency, adjust innovation cycles according to market demand, and provide clients with new services based on the data,” affirms the expert.
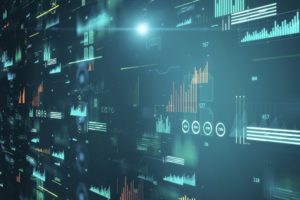
Companies must master the digital thread, which is the traceable dataflow that connects all phases in the lifecycle of a product or service
Managing the entire lifecycle of a product from a single platform with a constant flow of information in all directions means that each step in the process can improve the product quality, enabling companies to prevent errors in engineering and conceptual specifications from occurring in the early phases; accelerate application of the changes in manufacturing and the market launch; increase efficiency when collecting and analyzing data from the design and manufacturing processes; and reduce costs by using cloud-based services. Industries can therefore develop the appropriate machinery, optimize the manufacturing pr
ocess with a tight schedule, and provide effective and productive solutions.
In addition to this, the benefits when communicating with every provider, team member, and department through integration on a single platform must be noted, as it allows every participant to trace the product from ideation to its removal from the market.
Currently, just 21% of companies share ownership and use of the digital thread amongst the business departments outside of IT, while 50% expect that the IT department will be responsible for developing and maintaining it. However, according to Carlos Gallego, these tasks depend on multiple functions and systems. “Each part of the business will own its respective segment of the thread. That is why support from management and effective business leadership are critical to the success of this transformation,” he claims.
Technology applications
Developing the digital thread requires implementation of a range of tech tools, notable among them are CAD systems (computer-assisted design), Product Data Management (PDM), and Product Lifecycle Management (PLM), in addition to advanced analysis tools.
Integrating IoT technology into PLM systems will in turn enable management of the entire innovation process, product engineering, and updating from a single platform which stores the data from all the permanently connected creation phases.
One of the fundamental factors is to protect and ensure continuity of the digital thread in every stage, from the outline—where the data and their management and protection are key aspects—to the prototype and subsequent industrialization. “PLM systems, which manage products and product component traceability, require data integrity throughout the lifecycle, from design to manufacturing,” says Gallego.
It is therefore considered essential that the correct security policies not only be applied in IT environments and when accessing these environments, but also in industrial networks themselves. “Today industrial security and cyber security go hand-in-hand, and the key to success is integrity of information and manufacturing processes. ‘Security by design’ must be the risk management model in the digital thread model,” he suggests.
In fact, a digital thread can now be created that connects multiple ERP, PLM, and other systems spread throughout a supply chain with interfaces or a single shared database. “But security must be guaranteed from the start. That is the major challenge,” explains the consultant from Accenture, for whom technologies like blockchain provide a challenging alternative in this regard, as their ability to validate all data throughout the supply chain can guarantee precise, untampered information.
In expansion
The application and improvement of various types of technology have enabled the digital thread to expand its scope of operation. Initially, it was limited to the aerospace sector, which has an extraordinarily complex supply chain given the number of providers involved in designing, manufacturing, and assembling an aircraft’s materials. “However, data analysis and computing abilities, in addition to current connection infrastructure, have allowed the digital thread to be applied to almost any industry type,” says Carlos Gallego. He cites automobiles, energy, capital good manufacturing, and utilities as the sectors that are progressing the most in the application of the digital thread and data usage to improve their processes, thanks to their strong commitment to innovation and a greater ability to raise funds for this purpose.
To be fully implemented in Industry 4.0, the right infrastructure needs to be in place to gather data from a number of sources and perform analyses. This, in turn, requires a significant financial investment, claims the expert, who believes that once this essential requirement is achieved, the primary operational challenge in developing the digital thread is data governance and subsequent management, considering that “each of the thread’s segments can be implemented in accordance with the priorities and level of maturity of the business or function involved. However, there must be only one owner of the data governance so that it is not open to interpretation and can be unique.”
Looking toward the future, companies must be able to share these complex, unstructured data with their entire expanded value chain, including clients and providers, promoting the secure exchange of information while maintaining ownership of design, construction, and maintenance. “This shared digital thread model raises serious questions and challenges concerning how the companies who own the product design and the manufacturing methods can share information accurately and securely with all their partners in the supply chain,” notes Carlos Gallego.
This article was written with the participation of…
Carlos Gallego is Managing Director and Head of Industry X.0 at Accenture in Spain, Portugal, and Israel.
He leads Industry X.0 in order to help industrial companies take advantage of digital opportunities and abilities.
In his 25 years of experience as a consultant, he has implemented transformation programs with complex changes in business and technology processes for industrial, transportation, and infrastructure companies.
An ICAI industrial engineer—specializing in Industrial Management and Organization—he studied in the Executive Development Program at IESE (Universidad de Navarra) and the Digital Business Executive Program at ISDI.
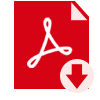