admin | 15/07/2021
The role of green hydrogen within the framework of the European Commission’s strategy for the reduction of greenhouse gas (GHG) emissions and the economy decarbonization process will be decisive.
This article focuses on the green hydrogen facilities. We will briefly analyze, given the characteristics and properties of hydrogen, how the applicable concept of safety must go beyond merely complying with the legal requirements, industrial regulations, technical norms or design standards. Doing that will require the experienced use of advanced tools to identify, assess and manage risks, which will serve as support for administration and decision-making.
The goal of all stakeholders involved in the industry associated with green hydrogen (operators, users, administration, insurance companies) is to attain the highest levels of safety: both in design and engineering, and in operation and maintenance, ensuring the minimization of accidents at the facilities and, as a result, operational and business continuity.
The production of hydrogen and the strategy of the European Commission
Today, 95% of the hydrogen produced in the EU is obtained primarily from steam-methane reforming with associated CO2 emissions (approximately 330 g CO2eq/kWhH2)2. It is known as gray hydrogen or “fossil-derived” in the strategy of the European Commission3.
This process can be complemented with CO2 capture, use and storage to obtain blue hydrogen, which has a 70% – 90% smaller carbon footprint. Most of the remaining 5% of the current production is obtained as a byproduct of the chlorine-caustic soda industry, which uses alkaline electrolyzers.
The electrolytic method has experienced very quick growth as a result of community and national policies. But to classify hydrogen as renewable (green), the electricity must have that characteristic, reaching carbon footprints of less than 30 g CO2eq/kWhH2. With a certain dose of reality, the Commission identifies “low-carbon hydrogen” as having a significantly small carbon footprint, whether produced by methane reforming with capture or by partially renewable electricity.
Today, hydrogen is used primarily at refineries to eliminate contaminants and produce quality products to meet demand (33%), manufacture ammonia (27%) and methanol (11%), and produce steel through direct reduction of iron minerals (3%). A total of 64% of the hydrogen production is onsite, captive, used in processes at the same factory.
The objective of the European Green Deal is to reduce greenhouse gases (GHG) emissions by 50% in 2030, which requires a rapid decarbonization process in the economy. To do that, among other lines of action, the European Commission the European Hydrogen Strategy (COM (2020) 301 final) published in July of this year, under which green hydrogen production with water electrolysis using renewable electricity is the key technology that will enable the penetration in the energy system of growing quantities of it in different forms known as Power-to-X.
This strategy aims to make hydrogen an intrinsic part of an integrated energy system that would have, in 2030, at least 40 GW of electrolyzers producing 10 million tons/year, and in which hydrogen would be the primary pillar of a decarbonized energy system and the raw material for industrial processes such as synthetic fuel manufacturing.
Figure 1 shows this concept, in which the resources for obtaining hydrogen are diverse, from natural gas and biomethane to renewable electricity. The priority is, of course, that most of the hydrogen should be renewable (green), obtained through electrolysis with wind-generated and solar electricity, as that is the option most compatible with the objective of climate neutrality by 2050.
What are the most relevant properties of hydrogen regarding safety and other fuels?
Hydrogen is a nontoxic, colorless, and odorless gas, classified as an extremely flammable gas according to the applicable regulations. In fact, to trigger the ignition of hydrogen, it takes 15 times less energy than for natural gas. And the range of concentrations in the air in which hydrogen is flammable, with a flame visible to the human eye, is 10 times greater than for gasoline.
It has a very low density. It is 14 times lighter than air and 22 times lighter than propane (Figure 2), and it dissipates very quickly. In case of leaks, it rises and dissipates quickly (at over 20m/s), unlike, for example, with propane leaks or other fuels, which tend to gather near the ground as they are denser than air. In any case, explosion risk assessments including the appropriate measures (equipment suited for use in classified atmospheres, ventilation, etc.) must be conducted to guarantee proper prevention of the risks of explosion.
Hydrogen combustion has some relevant unique characteristics.
- The self-ignition temperature, the lowest temperature at which a substance ignites spontaneously without the need for a spark or flame, is very similar to that of natural gas and much higher than gasoline vapor (Figure 3), which is a benefit in terms of safety.
- Additionally, hydrogen has a wide range of concentrations in the air in which ignition can occur (flammability range, between 4% and 75% by volume), much greater than that of other gaseous fuels (Figure 4). However, the concentration of hydrogen from which the mixture is flammable (the lower limit of flammability) is greater than the concentration of propane and gasoline vapors, which is also a point in its favor in terms of safety.
- The required energy, in optimal combustion conditions, to start combustion is much lower than for other fuels. So just a small spark could initiate combustion (Figure 5), which must be taken into account when putting together equipment that can act as potential sources of ignition, despite the fact that the high rate of dissemination plays in our favor, when necessary.
- Finally, hydrogen combustion produces a flame that is invisible to the human eye, so gas and flame detectors are used, along with heat vision cameras to detect it. The need for this equipment is significant because the thermal radiation produced does not produce a feeling of heat, as it is mostly in the UV range.
These analyzed properties give the industrial facilities that generate, process, and store hydrogen a certain level of risk associated with vulnerable elements (people, environment, and industrial facilities or assets), caused by undesired events, meaning it is necessary to provide sufficient safety barriers, as well as adequate risk management to avoid them or minimize their potential consequences.
Safety management in the green hydrogen industry
The main goal of all stakeholders involved in the industry associated with green hydrogen is to attain the highest levels of safety: both in design and engineering, and in operation and maintenance, ensuring the minimization of accidents at the facilities and, as a result, operational and business continuity.
Given the characteristics of hydrogen mentioned above, the applicable concept of safety must go beyond merely complying with the legal requirements, industrial regulations, technical norms or design standards. It also requires the experienced use of advanced tools to identify, assess, and manage risks as support for administration and decision-making.
This criterion is applied currently by the operators of facilities that produce hydrogen by other means (particularly the ‘gray hydrogen’ produced with methane vapor) in refining and the chemicals and petrochemicals industry. The arrival of new players in hydrogen production in different sectors undoubtedly requires replicating the high standards of safety put in practice by these activities.
To reach these high standards of safety, a brief discussion follows on the primary tools available and applicable in managing risks in the industry in the different stages of the life cycle at the facilities (Figure 6).
Many of them are not only common practices in the industry, rather they are requirements of the insurance industry designed to minimize the risks of an undesired event or inability or stoppage in the process causing damage or losses of production.
Design Safety
In the design and engineering stage (conceptual, basic, and detail), the plants must be configured with intrinsic safety to reduce the risk both inside and out to a minimum. It is imperative in this stage to conduct an exhaustive risk analysis and apply proper techniques to manage all possible hazardous situations.
Various different tools (HAZID, HAZOP, SIL Analysis, LOPA, FMECA, QRA, BRA, FERA, FIRE&GAS, ALARP, BOW-TIE, ATEX, Human Factors Engineering, Human Factor Risk Analysis (Human HAZOP, SCTA), etc.) can be used depending on the particular engineering phase, the project being carried out, the end objective and the risk management policy which the project developer and engineering have defined as being appropriate for attaining these objectives. The application makes it possible throughout the life cycle of industrial facilities to obtain significant benefits in safety, such as:
- Identifying hazardous situations originating internally or externally that can lead to a scenario of accidents, which involve hydrogen or other present substances, or in any of the operations in the plant construction and operations phase, including those caused by the Human Factor.
- Assessing the damage caused by potential accidents, quantifying the effects and consequences on vulnerable elements (people, environment and assets)
- Determining the probabilities of occurrence of the events indicating a hazardous situation and their different potential evolutions.
- Quantifying and assessing the risks.
- Identifying the preventive and mitigating safety barriers to roll out to control the risks at acceptable levels.
To name just a few practical examples of application of some of these tools for the design phase or best practices recommended by the insurance companies, and considering the properties of hydrogen mentioned above, we have the following analyses:
- SIL analysis, which enables the design and implementation of the life cycle of the Safety-Related Systems (interlocks) in accordance with the best practices regulations on Functional Safety, for proper design, operation, and maintenance of these systems with safety and reliability criteria.
- Fire&Gas, aimed at proper design and location of the fire and hydrogen detectors as a safety barrier to identify potential hazardous events at early stages, activate the necessary response mechanisms, and mitigate possible consequences. These Fire&Gas studies make it possible to ensure the different types of sensors are placed optimally, where the design of processing measurement signals and their transmission is very important, to activate protocols quickly and effectively.
- FERA (Fire and Explosion Risk Assessment) is the most appropriate and optimal way of implementing and placing process equipment, particularly the critical equipment, based on the consequences and risks analyzed, determining their construction needs to support those adverse effects.
- BRA (Building Risk Assessment), to define the best location of the buildings and control rooms, as well as the parameters for their structural design to guarantee their integrity in the event they are affected by values of excess pressure and/or thermal radiation that require a special level of production of the people and facility control systems they house.
- ATEX Studies Classification of Hazardous Areas, Explosion Risk Assessments and Explosion Protection Document, in compliance with the obligation so of RD 681/03. Conducting studies of this type must consider the specific conditions of each facility, assessing in detail each possible source of ignition—one by one—in each classified area. As best practices, the implementation of NFC tags is starting to spread, including relevant information on the equipment, as well as in the area of ATEX, which facilitates the management of risks of explosion caused by electrical and mechanical equipment. Lastly, the assessment must take into account, again, the potential role of the human factor as the origin of sources of ignition.
- Human Factors Engineering, to verify that the design of the new facilities: a) complies with prevention standards; b) meets ergonomic criteria; c) guarantees accessibility to critical elements in emergency situations; d) minimizes risks of accident potentially caused by the human factor; d) maximizes the operability of the facilities. Undertaking this type of analysis in the design phase (conceptual, basic and/or detail) eliminates the cost of implementing corrective measures once the facilities have been built and delivered. HFE can be conducted by including HFE specialists on the design teams, or by reviewing 3D models remotely for the projects as they are generated in the different phases of development of the Project engineering, or though HFE sessions, similar to the HAZOP sessions.
Operational Safety
Operations require the implementation of process safety management systems that guarantee proper functioning of the assets. These systems are based on two key pillars: the organization’s commitment to safety and knowledge and management of the risks.
The common practice in the Oil&Gas and energy sectors is to adopt and implement Process Safety Management System (PSM) standards primarily to avoid the occurrence of accidents in facilities in which substances of a hazardous nature, such as hydrogen, are used, stored, produced, and/or handled.
PSM is based on the development and implementation of the following cornerstones of safety:
- Achieving unwavering organizational and personal commitment and leadership in process and operational safety.
- Understanding the risks and hazards deriving from the chemical processes to identify and assess
- Managing risk with tools that enable monitoring, follow-up, alarms, as well as available and reliable safety barriers.
- Learning from experience by incorporating the lessons learned in review and improvement.
PSM implementation will cover key aspects and issues related to safety in the life cycle of the facilities (Figure 7) such as:
- Safe design, engineering, and construction
- Hazard assessment
- Efficient alarms
- Effective process control
- Appropriate procedures for commissioning and operational startup of facilities
- Management of modifications
- Inspection, testing, and maintenance of equipment
- Personnel training
- Relationship with providers and suppliers.
- Communications in the organization and between its managers
Human Factor Risk Analysis
The unfortunately well-known quarterly industrial accident analysis shows a clear lesson: in most of them, a crucial role is assigned to causes related to human error.
Despite that, paradoxically, the “human factor” has not played the relevant role that corresponds to it in the risk analyses until quite recently. The arrival of Human Factor Risk Analysis methodologies, such as the safety critical task analysis (SCTA), Human HAZOP, and other systemic approaches has alleviated this deficit to a certain extent. With tools like these, the apparent multiplicity of deviations that humans can introduce into the systems is configured through parameters, and the risk analysis is complemented, so that corrective and control measures are adopted (as shown in the example in Figure 8), minimizing the probability of anomalous behaviors (mistakes, distractions, lapses or violations) and, above all, minimizing the importance or consequences of those anomalous behaviors.
It is therefore essential to understand the real determinants that could lead to failures in operations at the facilities (PIFs or Performance Influencing Factors). Human Factor Risk Analyses systematically analyze the deviations that operators can introduce into the system, taking into account the PIFs, assessing the anticipated consequences (accidental or otherwise), considering the available safeguards and defining the corrective and control measures that need to be introduced. These corrective measures to be introduced, which are the true reason behind conducting these analyses, can cover the implementation of process safety elements, indicators, relocation of equipment or controls, etc., and not only training and information or organizational measures.
Reliability and Maintenance
The integrity of a physical asset is its ability to carry out its functions effectively and efficiently, contributing to meeting the objectives of individuals, collectives,or interest groups, while preserving their status and conservation, safeguarding at all times the environment and safety.
This vision of the operational behavior of a particular piece of equipment, system, or facility is based on integrated management of the following aspects during the operational stage of the assets at a hydrogen plant:
- Performance of the physical asset or level of effectiveness achieved by an asset in terms of availability (ability to meet the functional demand of the physical asset), reliability (ability of the asset not to fail to fulfill its functions), and maintenance (ability to preserve and recover the functionality of the physical asset in the event of degradation processes or damage).
- Risk associated with operating the physical asset, which is the damage that could occur during a particular interval of time as a result of the appearance of damage, must be managed appropriately with a proactive approach that prioritizes preventive actions over reactive behaviors, minimizing negative impacts that could arise from that damage.
- Incurred cost, used to obtain a sustainable profit over time, constantly generating revenue that exceeds the costs associated with undertaking the business activities.
Asset integrity requires adopting optimized maintenance and reliability strategies for the equipment, infrastructures, and safety barriers, with tools such as those established in standard ISO 55000 for facility optimization.
Each facility and operating environment requires an analysis process to define the activities, techniques, tools, and implementation sequence that is best suited to each case (Figure 9), taking into account the operational reality, objectives, interests, capability and resources, degree of organizational maturity, and available period of time.
For example, the following, among others, are highly useful and regularly used in the Oil&Gas and Energy industrial sectors, and are recommended by insurance companies:
- RAM Studies (Reliability, availability, and maintainability), to quantify the probability of potential equipment failures, estimating the availability of the hydrogen generation plant and focusing maintenance actions with an optimal cost-to-profit ratio.
- RCM Studies (Reliability-centered maintenance), used for optimal assignment of available resources for the maintenance of a facility, focusing on the most critical assets for the functionality of the facility and, as a result, for business continuity. RCM determines the type and level of maintenance that must be used for the equipment based on the risk associated with potential failures.
- RBI Studies (Risk-based inspection), to monitor the status and evolution of the static components at the facility, based on conducting inspections to verify the mechanical status and integrity of the equipment based on the risk introduced by each element. It prescribes a series of inspections and tests to obtain as much information as possible on the remaining life of the elements and equipment.
An appropriate strategy of asset integrity and application of the tools will increase the reliability and availability of a hydrogen plant, minimizing risks and guaranteeing the return on investment made in its implementation.
Emergency and business continuity planning
Additionally, and no less important as a key aspect as a safety barrier, is the necessary planning for emergencies and business continuity (Figure 10), which will establish an organized response from all human and material resources to limit consequences in the event of an accident.
Regarding the organization and human resources, it is imperative to establish the operations in the emergency plan, as well as the action procedures to be followed. With regard to the latter, the insurance industry also recommends creating and implementing the Fire Pre Plan for each accident scenario that could involve hydrogen or other substances such as oxygen, as well as in the process equipment (electrolyzers, compressors, storage, etc.). The Fire Pre Plans provide, for example, a detailed map of the area and scope of consequences, available firefighting/emergency resources to be used or mobilized, nearby affected hot or critical equipment, action instructions for operational personnel or emergency teams.
In addition, elements such as passive and active fire detection and extinguishing systems are key aspects in the design of the facilities and the emergency response. In this sense, operators must consider the specialty risks of hydrogen when defining the protection and systems. Planning based on continual improvement requires theoretical and practical training for key personnel, conducting drills, and simulations.
And, finally, at a higher management and operational level than crisis management and emergency plans themselves, business continuity plans will make it possible to identify the potential threats to plant operations and establish suitable continuity strategies to guarantee the resilience of the green hydrogen facilities.
Conclusions
In conclusion, as can be seen, the application of all these tools to identify, assess, and manage risks at green hydrogen facilities will make it possible to create intrinsically safe facilities, identify and assess the risks (zero risk does not exist), guarantee proper management, minimize the occurrence of accidents and establish the response mechanisms for better asset availability, contributing to business continuity.
To that end, it is extremely important that the promoters and operators of green hydrogen projects prioritize safety and risks throughout the life cycle of the projects with the support of specialists in the different areas described.
In this sense, fulfillment of the objectives of the Commission and project promoters depends, among other factors, on the creation of a safe and reliable green hydrogen industry that minimizes the appearance of ‘showstoppers’ through sound and experienced management that is perceived as such by all stakeholders.
Authors:
Gabriela Reyes Delgado. INERCO Industrial Safety Department Head
Juan Santos Remesal. INERCO Industrial Safety Division Manager
Pablo. Navarro González. INERCO Risk Prevention Managing Director
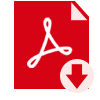