Design and construction have evolved significantly in the last 15 years, initially driven by new demographic and social demands. Evolution of technology has played a fundamental role in this progress, and techniques like 3D printing and robotics are bringing the mechanics of construction closer to automation. Although, like all recent innovations, it is still being standardized and certified. Promising steps have already been taken to introduce cybernetics into infrastructure development.
The construction sector is facing a positive, yet highly demanding era. Both the residential and industrial construction sectors are forecast to grow in 2020. According to studies by the Institute of Construction Technology of Catalonia (ITeC), investors still view Spain as a profitable market, and two of the market niche sectors with positive growth forecasts are logistics and offices. Despite the fact that many processes have remained unchanged—except in the development of traditional machinery—and, compared to other sectors, this sector’s degree of digitalization is quite low. The technological wave that is transforming other sectors is beginning to reach the construction and infrastructure industries.
As in the majority of industrial processes, the trigger for this transformational shift was task automation, which little by little has been successfully implemented in different project phases. Although the cost reduction it brings is notable—mitigating costs by up to 35%—there are other reasons to choose task robotization, as Vicente Ramírez, an architect at Be More 3D, explained. “For quite some time, technological innovation has been focused on increasing output, but also on reducing CO2 emissions and using new materials,” he stated. The mechanization of building processes begins with the creation of different components comprising a piece of infrastructure and runs until its final assembly.
Although 3D printing is a tool with a long history, first tested successfully in 1984, it was in the 21st century when it had a monumental impact on fields like medicine, art, and food. It only became an option for construction in 2004 when professor Behrokh Khoshnevis (University of South Carolina), an expert in the field, produced the first wall using this technology. It is now expected to pave the way to the future of construction. “3D printing is becoming increasingly common as the methodology is improving and becoming more affordable. Our research mainly focuses on the use of concrete. It could theoretically be used for any kind of construction. Although there are still technical aspects that need to be analyzed,” explained Timothy Sandy, an engineer at NCCR Digital Fabrication in Switzerland.
For quite some time, technological innovation has been focused on increasing output, and also on reducing CO2 emissions and using new building materials
A promising start
3D printing in construction is done with contour crafting, a technique developed by professor Khoshnevis, which overlays layers, creating subcomponents and complete structures. According to Sandy, this opens all of the possibilities of manufacturing to an architect’s creativity. “New technology allows for new geometries. Therefore, by using digital manufacturing, every design element in a building can be custom built, following the exact requirements of its final location,” Sandy asserted. “With regard to planning, it is the same as a conventional system,” Vicente Ramírez added, “a new range of possibilities is opened up in the design, but you’ve also got to create an outline while thinking about what you want to print. That’s how we can get the most out of this technology’s strong points.” The result of that creative freedom was on display in early 2020 at the Scottish design museum V&A Dundee, which, with the help of Gramazio Kohler Research and ETH Zurich, displayed a timber structure (Up-Sticks) made of 2,000 spruce planks and beech dowels, inspired by traditional building methods, but created using computational techniques and robotics technology for its design, drawing, and installation.
Outside of the sphere of exhibition, several initiatives have been implemented. In Spain, the company Be More 3D, founded in 2014 by entrepreneurs from the Universitat Politècnica de València (UPV), was able to build the first home on-site with a 3D printer from Spain. Ramírez, one of the project supervisors, assured, “it was a massive success. We started out printing in plastic and in less than a year we had moved on to printing with concrete. In the beginning we printed small parts to test the machinery and the materials developed with UPV. Then we started printing the home.” The final texture has proven to be extremely durable in harsh weather. “We used a micro concrete that can be employed between 0 and 50 Celsius (32 to 122 degrees Fahrenheit). In late 2019, we built the first 3D home in Africa and tested it in the extreme temperatures there. It performed well, although this is not recommended by the Spanish technical building code,” he stressed.
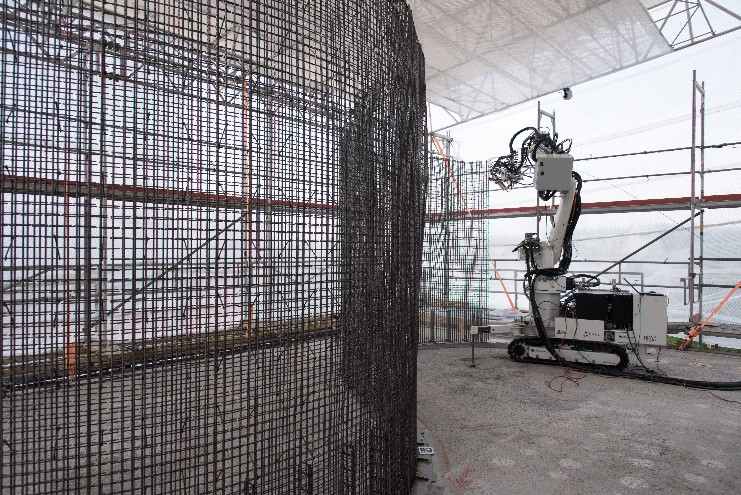
3D printing can reduce waste by building slabs with up to 65% less concrete than traditional slabs.
The advantages of this kind of manufacturing are undeniable: cost reduction, the freedom to create any shape, customization, and reducing waste, dust, and noise by up to 85%. Despite
this, the sector remains reluctant. “As always with new, disruptive technology on the market, the main barriers to its entry are fear and lack of knowledge. With pilot projects like the ones in Valencia and Morocco, that barrier is being broken down,” he explained.
He also made it clear that this technology is not here to replace humans, but rather to enhance their work. “It complements traditional construction perfectly, as the printer only makes the load-bearing walls, the structure. After that, all the workers come into play as they would in a conventional building project. It also reduces occupational hazards, since people don’t have to work at height to make the structure,” he explained.
For now, the creation is limited to this framework. Although further research is progressing quickly. “I think that even printed furniture will have a market in time. In any case—fortunately—humans will always need to be there. With regard to the challenges we are facing, we are currently developing a new technology: a multi-printer able to print buildings up to five stories tall,” he added.
Robotics partners
For decades, process automation has been carving out a space for itself within the construction industry. Starting with simple mechanization to make work easier, the last few years have witnessed a robotization trend that—in conjunction with 3D products, which can now print 60 m2 spaces in no more than 8 hours—is being introduced into an autonomous manufacturing system that has notably improved accuracy and productivity. All of this evolution is leading to a level of efficiency that was until now unimaginable. “Our robotics technology is appropriate for repetitive tasks where the force required is for loads ranging from 5 to 20 kg (11 to 44 lbs). Although they still have some difficulty performing certain tasks on-site, initial evidence shows that they can be used to build highly precise structures, even structures that are impossible to create by hand,” Sandy said.
This technology can also be used as a tool. “Since robots are used in this scenario, it’s not just that something new is created, but the risk of injury is also reduced, since the robot does all the heavy lifting,” Sandy explained. Convinced that “robotics has no limits,” Ramírez added that it will be very beneficial for union workers. “It will certainly create new jobs. If more homes can be built for the same amount of money, undoubtedly construction jobs will be created, in addition to new professions that have never existed before.” Sandy indicated that “the option for remotely-controlled machinery does exist, which will allow operators to work from safer, more comfortable work environments, which will be especially useful in digging jobs in extreme terrain.
The autonomous units are being integrated gradually, but full integration is almost guaranteed in the first few steps. “We are carrying out work that aims for partial or total automation of traditional machinery (excavators, cranes, etc.). Finally, robotic solutions are being developed that simply monitor the work site, generating extensive data about the status to feed BIM models to improve the project’s management and logistics,” Sandy concluded.
Other immersive technologies
The implementation of technology is not limited to the construction phase, and naturally, from project design to subsequent maintenance, a paradigm shift has occurred throughout the industry based on task virtualization and data collection to improve performance and optimize the time spent and the work quality. Some technology that is a part of this advancement includes:
– Building Information Modeling (BIM) is a system of modeling that centralizes all the information on a construction project. It is a major breakthrough over traditional design systems as it optimizes costs and generates modifications in real time without having to repeat design tasks with all the players involved. This technology is also incredibly useful in the subsequent infrastructure use phase, as it offers up-to-date, reliable information. Therefore, it is not only a planning tool, but also an overall management tool.
– Augmented Reality. According to Timothy Sandy, “solutions are being developed for augmented reality-guided building on-site, which can improve construction workers’ productivity as it makes the information from the digital model of the project more accessible and intuitive. They are also used to create modules that could not be built with conventional methods. This technology can leverage BIM models to improve performance and also to measure aspects of the site, obtaining in turn more data to feed the model and assist in planning and logistics. The augmented reality devices available (e.g., Hololens2) are limited in terms of field of vision, size, and brightness, but that should improve quickly in the coming years.”
This article was written with assistance from…
Vicente Ramírez is the Director of Operations and R&D Projects, logistics in new project implementation, client management, and international expansion at Be More 3D. He graduated with a degree in Technical Architecture from UPV and completed an advanced vocation qualification in construction project application and development.
In 2018, he received a master’s degree in Start-Up Administration from Universitat Politècnica de València.
Timothy Sandy graduated with honors from Carnegie Mellon University in the United States with a Mechanical Engineering degree in 2008. He spent three years working in a program at Eaton Corporation where he developed products for the aerospace, auto, and commercial transportation industries. When he returned to Switzerland he completed a master’s degree in Robotics, Systems, and Control from the ETH Zurich in 2013. Since September 2014, he has been working with the National Centre of Competence in Research (NCCR) Digital Fabrication, where his research focuses on machine learning, artificial intelligence, and robotics.
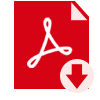