As part of Risk Management and to protect, among other aspects, the company’s assets from the risks that may affect its business and the losses that may result, such risks must be prevented, avoided or mitigated.
This time we are going to focus on fire risk mitigation, and to do so we will have fire protection means (medios de protección contra incendio – MPCI) as passive protection (sealing of cable passage holes, fire barriers, fire walls), manual extinguishing means (extinguishers, fire hose cabinets, hydrants) and automatic extinguishing means (fire detection, sprinklers, deluge systems and others).
Companies typically make a very significant investment in these types of systems, so a failure or deactivation of these systems without any kind of control results in the affected plant or area being unprotected and consequently, in the event of a fire, the damage can become catastrophic.
This is why we must ensure that these systems are not only well designed, installed and maintained, but also operational at all times.
However, it is sometimes necessary to deactivate these types of fire protection systems (protección contra incendios – PCIs) due to the need to carry out:
-
-
-
- Specific works in the factory.
- Find out why they break down, deteriorate, or, if necessary, expand these PCI systems.
- Need to carry out maintenance tasks on these.
-
-
In this case, alternative safety measures must be taken so that in the event of a fire, it can be controlled.
To do this, it is necessary to develop and implement a procedure called “deactivation of fire protection” in order to ensure that the disconnection of the systems is safe, and to implement a series of alternative safety measures for control/mitigation in the event of a fire.
When developing such a procedure, the different risk scenarios that could occur, the systems that could be deactivated and the alternative security measures required for each of the scenarios, must be considered.
Written procedures for the control of the deactivation of MPCI
Each company will develop their own procedures based on the intrinsic risk of their particular business, the size of the plant and the types of PCI systems in place. The following aspects must be clearly defined in the procedures:
- Types of deactivation : Planned (maintenance work) or unexpected/emergency (breakdown).
- Deactivation time: Keeping it to a minimum, even with preventative repairs to the system, and restoring protection availability as quickly as possible.
- Departments: Production equipment and facilities that can be left unprotected by the deactivation of existing PCI means.
- Clearly establish additional safety measures such as those listed below:
-
-
- Reinforce preventive measures in affected areas such as:
- Halting any potentially dangerous operations being carried out in the affected area.
- Rigorous prohibition of smoking and its enforcement in the affected area.
- Not performing hot work.
- Paying extra attention to order and cleanliness in the affected area.
- …
- Reinforce preventive measures in affected areas such as:
-
-
- Reinforcing fire protection with alternative fire protection measures, necessary manual protection, or other systems.
- Establishing inspection rounds of the affected area, with the necessary frequency depending on the degree of danger associated with the activity. This is usually recommended to be done every half hour.
- Establish the departments or persons involved (supervision, security, maintenance, insurance company, etc.), their responsibilities and the communications to be carried out.
- Ensure that PCI systems are operational once the work is completed; correctly complete the procedures for “decommissioning and reactivation of PCI systems” informing the affected departments that the MPCIs are already operational in order to be able to resume the plant activity at 100%.
Permit for disconnection
To properly implement this type of MPCI deactivation procedure, it is necessary to have a work permit to manage and control it. This permission must include:
-
-
- Information on the reason for disconnection.
- The areas affected.
- The PCI systems to be deactivated.
- Necessary fire prevention and protection measures.
- Identification of the person authorizing the deactivation.
- Date and time at which the MPCIs are to be deactivated.
- Identification of the person who will be monitoring the disconnection process.
- The jobs, the safety measures during this time.
- Date and time of completion of work and reconnection of PCI systems.
- And confirmation of the successful recommissioning of PCI systems.
-
By way of conclusion
A company that has invested in improving fire protection levels by installing extinguishing means, but where such extinguishing means are disabled without any controls being applied, will result in a false sense of security and, in the event of a fire, the consequences could become catastrophic. For this reason, it is completely necessary, if there are fire extinguishing means to hand, to prepare and implement these types of deactivation procedures in a coordinated and safe manner.
As risk managers of a company, and whenever we have fire protection in place, we must ensure that this type of procedure is in place and properly implemented.
Article author:
María Teresa Queralt, Technical Department Expert at MAPFRE GLOBAL RISKS.
Keed reading… Fire prevention and management from space
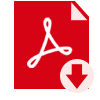