admin | 14/07/2021
In recent years, the decarbonization challenge taken on by large industries within the framework of the SDGs has brought together partners in all business areas with the aim of achieving significant results by 2030. One of the most promising areas, in terms of the decisive effects and the path ahead, is industrial insulation, which could lead to energy savings of up to 15 billion kilowatts-hour and where the potential lies in the development of mineral wool.
The industrial sector is, together with transportation, the segment that could contribute the most to the energy sustainability goals that are on the agendas of governments throughout the world. As part of the Sustainable Development Goals established by the United Nations, and in particular in SDG7, numerous goals are addressed in this area: universal access, growth of renewables, international cooperation, etc. Another aspect that stands out is the promotion of energy efficiency technologies. Among them, insulation could be a significant change, as explained by the Spanish Association of Insulating Mineral Wool Manufacturers (AFELMA).
“Specifically, oil refineries, power plants, and the chemical industry would contribute towards 57% of these savings, and 61% of the reduction in CO2 emissions provided the right measures are taken. In this context, mineral wool is the ideal insulator because it allows a high degree of energy savings, reducing consumption to the minimum rationally possible and thus reducing the deterioration of the environment,” says Monica Herranz, secretary general of the association.
In Spain alone, if thermal insulation requirements were improved, up to 12.5% of the energy sustainability target could be achieved by 2030. “Correct insulation in industrial facilities can save 15 billion kilowatt-hours per year. To put this in context, this is equivalent to the amount of oil that would be needed to circumnavigate the Earth in a Boeing 747 at least 2,509 times,” the expert stated.
Investing in savings
According to the Ecofys study carried out by the European Foundation for Industrial Insulation, case studies and success stories show that the savings potential of process and system insulation in industry can reach 400 million euros per year in Spain. “In other words, 13,600 gigawatt-hours and 3.4 million tons of CO2, which is equivalent to the consumption of 1,200,000 homes or the CO2 of 1,700,000 cars. While these savings are possible, they require a total investment of 7.37 billion euros, of which approximately 1.65 billion would be in the public sector. A key piece of data taking into account the opportunity provided by the European Funds agreed for Spain in the framework of the Mechanism for Recovery and Resilience corresponding to the green transition,” AFELMA claimed.
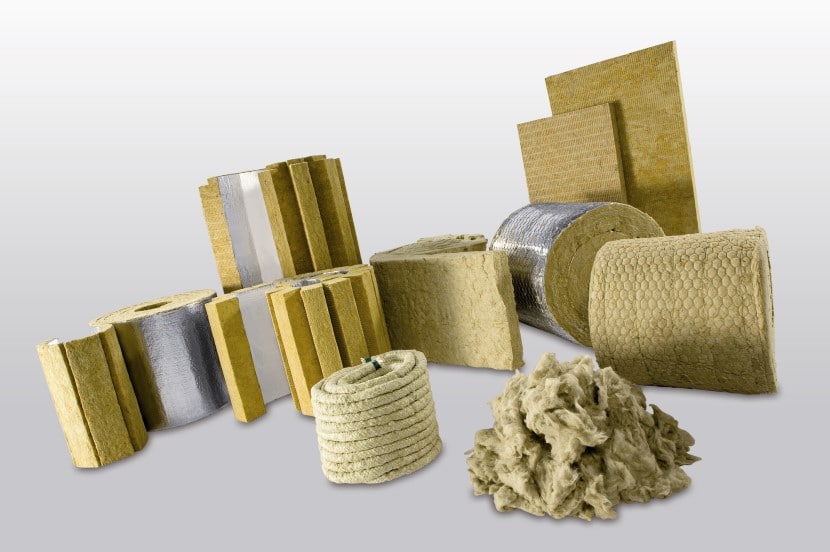
Depending on the application to be carried out, there is a wide range of products, glass wool and/or rock wool (both called mineral wool), for each respective case.
To meet the sustainability and efficiency commitments, not only must the basis of good insulation be included in the design and construction phases, but also the refurbishment and improvement of materials must also be promoted. “All the paths to decarbonization include refurbishment, and mineral wool plays a leading role in this.” This material, which is obtained from natural products—siliceous sand for glass wool, and basalt rock for rock wool—is made up of an interlacing of stone material filaments that form a fabric and hold air between them in a static state. This flexible structure makes it possible to obtain a product capable of providing a triple condition: acoustic insulation, thermal insulation and, due to its incombustible nature, protection against fire.
AFELMA points out the advantage of the triple protection—thermal, acoustic and fireproof—offered by mineral wool. “Mineral wool is the most widely used insulation product in Europe, and manufacturers are constantly working to improve its quality and performance,” they explained. It has a wide range of potential uses and positions: roofs, facades, floors, false ceilings, partitions, air conditioning ducts, protection of structures, enclosures, thermal insulation of pipes, equipment, tanks and hot surfaces that suffer energy losses. “In short, it is a sustainable, efficient, and suitable material for insulating all types of buildings and their facilities,” they noted.
In addition to mineral wool, there are other materials that can be used, which must always be new, properly packaged, and free of moisture before installation. These materials must have a certificate of origin and technical and safety data sheets. The fundamental characteristics that the insulating materials must provide are:
- Energy savings: with high thermal insulation, which hinders the flow of heat through the material.
- Optimal acoustic performance: facilitating the transformation of acoustic energy into kinetic energy.
- Safety: they must not burn or produce smoke, maintaining their thermal insulation capacity even at high temperatures.
The UNE-EN 14303 Standard specifies the requirements for manufactured mineral wool products used for thermal insulation of equipment in buildings and industrial facilities, with a working temperature range of approximately 0° C to + 800° C.
Other types of products that have been used in industry include:
- Cellular glass: Material made from fired glass powder, also called expanded glass. Used primarily as thermal insulation and fire protection.
- Elastomeric foam: Flexible closed cell foam thermal insulation specially designed for outdoor facilities. It acts as a barrier against water vapor and reduces the risk of condensation.
- Microporous material: Insulation product in the form of compact fibers or powder with an average interconnecting pore size comparable to or below the mean free path of air molecules at standard atmospheric pressure. Its working temperature is up to +1,000° C.
- Ceramic fiber: Lightweight, needlepunched blanket made from earthy alkaline silicate wool, which provides a solution to a variety of thermal management problems. It maintains its strength, flexibility, and thermal properties up to a temperature of +1,200° C.
- Aerogel: Flexible industrial insulation blanket for high temperatures, made of silica aerogel, and reinforced with non-woven fiberglass filler. It operates at temperatures up to +1,000° C.
Risk prevention
The industrial fabric of Spain, in terms of insulation, is not subject to any mandatory regulations, compared to the residential, which is regulated by the Technical Building Code (CTE), which AFELMA points out as essential in defining the technological level of the region.
“Although the sector is becoming increasingly aware, studies have found that at least 10% of the surfaces of the facilities are not insulated or are deteriorated. The remaining 90% could reduce their energy losses by up to 75% by investing in improved insulation. The investment is usually as minimal as possible because it only focuses on the surface temperature to avoid personal injury, as well as the basic needs of the industrial process,” Herranz stated. “The insulating properties of mineral wool, including its fireproof nature, contribute to risk prevention and facilitate safety conditions in the development of industrial activity, as do the acoustic insulation, thermal comfort, and maintenance of indoor air quality they provide.”
Article contributor:
Mónica Herranz has been the general secretary of AFELMA since 2004. For 13 years prior to this, she was responsible for the Technical Secretariat of ANDIMAT, National Association of Insulating Materials Industrialists, meaning that she has spent almost all her professional life in the world of insulation.
AFELMA is the Association of Spanish Manufacturers of Insulating Mineral Wool that represents all the companies producing mineral wool in the Spanish market. It was created in 1979, as a non-profit organization, to publicize the quality of mineral wool products and promote the proper use of thermal and acoustic insulation and fire protection.
Its main objective is to improve the quality of buildings in Spain, promote the well-being and quality of life of people, and contribute to a healthier and more sustainable future.
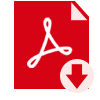