admin | 25/09/2018
The clean energy production infrastructures most on the rise are wind and photovoltaic power. Both tend to have gigantic structures, which cause certain challenges for their maintenance and running. This is the field of expertise of Arbórea Intellbird, a company with a young team of engineers from Salamanca, who have created a digital platform which combines specialized software and the Arachnocopter drone used for aerial inspections. This is allowing for the digitalization of wind turbines, large photovoltaic installations or electric power line inspections.
The digital era
Some authors cite that there were almost one million manuscripts housed in the legendary Library of Alexandria, in its most prosperous era. 2000 years ago the mecca of human knowledge was stored in this enclave, where a lucky few could go to find enlightenment. Today, a by no means negligible portion of the planet’s population has a device in their pocket capable of providing instant access to a dizzying array of books and technical documents. This is a far greater volume of information than the legendary library from the Ptolemaic times held. Universal and instant access to knowledge is propelling us towards something similar to a new Renaissance.
All of this has been made possible thanks to the enormous progress seen in microprocessor technology. Their transformation into an object of mass consumption has led to their miniaturization, continual improvement and lowering of their price. The impact of this progress in handling silicone has ushered in pocket-sized supercomputing. The internet of things extends to the objects in our daily life. Being able to manage and analyze huge amounts of data has accelerated with the help of artificial neural networks which can learn and generate increasingly smarter answers.
These technological advances are clearly based on electrification processes. Transport is slowly joining this electrification, which will inevitably increase its demand. It is important to encourage more and more sustainable ways of generating this electricity. The clean energy generation infrastructures most on the rise are wind and photovoltaic power. Both tend to have gigantic structures, which cause certain challenges for their maintenance and running. This causes certain challenges for their maintenance and running, which become more complicated the bigger the blades or the surface area covered by gigantic solar farms. Optimization of inspections and repairs predictively is one of the keys to progress in this area. In fact, the digitalization and automation of these processes is beginning to prove essential in order to make electrification underpinned by renewable energy generation structures possible. (1)
According to figures from Bloomberg New Energy Finance, the wind power generation sector is one of the fastest growing industries in the world. With over 268,000 wind turbines installed worldwide by the end of 2014 (2) and 539,123 MW, at the end of 2017, according to figures from the Global Wind Energy Council (GWEC).
The use of large wind turbines is growing due to the price of energy, environmental considerations and the increasing efficiency of these machines. According to figures from Bloomberg New Energy Finance, the wind power generation sector is one of industry’s most rapidly growing segments worldwide. With over 268,000 installed wind turbines worldwide at the end of 2014 (2) and 539,123 MW, at the end of 2017 according to figures from the Global Wind Energy Council (GWEC).
Typical wind turbines, designed to produce 1-3 MW of electricity have a three-bladed configuration, which is the industry standard, of 30 to 50 m long. The wind energy industry tends to replace them with ever larger and more efficient machines, with blades up to 80 m long that can generate 7 MW.
Wind turbine blades have a sophisticated design with complex curvatures. Based on multilayer structures of varying thicknesses, they are built from materials made of layers of fibers and artificial resins, and occasionally reinforced with wood. These structures are designed to be in operation for a minimum of 20 years. However, in practice, they present certain difficulties: The blades can be damaged by particles in the wind and sometimes even by strong tension and twisting. This causes a complex series of faults which vary based on the design of the blade, the model and even the serial number. The differences in the manufacturing process and the characteristics of the materials or designs vary considerably, in an industry which has not been around very long and therefore lacks well-established standards based on past references.
The analysis of faults in the blades is a complex discipline which requires significant experience and in-depth knowledge of the design and manufacturing processes of these structures.
An application of the technology is needed that allows us to ascertain the actual condition of these assets and to start a sustainable predictive maintenance procedure. This will remove dangerous uncertainties from the picture and will stabilize the relationship between manufacturers, developers and insurers.
The use of predictive maintenance programs for wind turbine mechanical, electric and electronic components is widespread in the wind energy industry, however, when it comes to blades, which are undoubtedly one of the critical components of this machinery, such programs are not extensively used. The sudden onset of catastrophic damage to blades, although infrequent, can be particularly severe.
The wind energy industry is advancing in the improvement of procedures for generating a future predictive maintenance of blades that allows for the establishment of early repair at low cost, based on the identification of faults in their first stages, in order to prevent large-scale accidents. The implementation of this type of technology is needed in order to correctly evaluate the risks and the sustainability of the insurer’s business in this sector. Up until now, the situation of wind turbine blades, a critical component, was one of dangerous uncertainty. The direct consequence of catastrophic damage, which occurs on a regular basis, is a devastating loss of cover for small developers and a possibly unnecessary rise in the cost of the premiums, not to mention bad business for insurers. An application of the technology is needed that allows us to ascertain the actual condition of these assets and to start a sustainable predictive maintenance procedure. This will get rid of any dangerous uncertainties and will stabilize the relationship between manufacturers, developers and insurers.
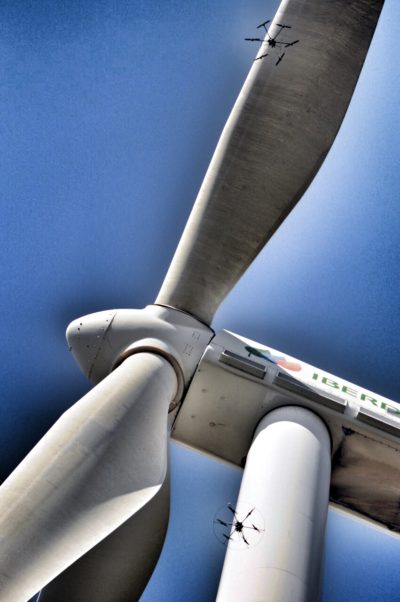
Filming a wind energy inspection from the air
This is the field of work of Arbórea Intellbird. The brainchild of a young team of engineers from Salamanca, who have created a digital platform which combines specialized software and the Arachnocopter drone used for aerial inspections, is helping to digitalize wind turbine, large photovoltaic installations or electric power line inspections. Its flight guarantees the safety of the wind turbine’s blades in a variety of countries such as Spain, Mexico, Chile, or even Japan, to cite a few examples. This small company which Iberdrola and the Spanish State teamed up with through CDTI (Centre for the Development of Industrial Technology) generates services to the main multinationals in clean energy. Promoting smart digital processing increases the efficiency and safety in large-scale production facilities, while simultaneously reducing running and maintenance costs. In this way an attempt is being made to speed up the expansion of renewable energy production as the path towards sustainability.
.
.
Inspection of blades with drones, first steps
In the first decade of the 21st century, progress in the drones industry started to tentatively focus on application in the wind energy sector. In 2010 the Spanish wind energy industry approached Arbórea Intellbird with the pioneering idea of creating a multirotor drone specifically designed to inspect wind turbine blades. The system was developed from the Arachnocopter platform, whose design began back in 2008. The Arachnocopter EOL6 was launched in 2012 with considerable success in the biggest wind trade show in the sector, the Husum Wind Energy fair in the north of Germany.
In 2010, the Spanish wind industry proposed Arborea Intellbird, the creation of a specific multirrotor drone for the inspection of wind turbine blades.
In order to evaluate the possible advantages of drone technology for wind turbine blade inspections, it is important to understand the sector’s needs and also the solutions the market provides: its differences and advantages.
Despite a global boom, the wind energy sector is not economically viable in some geographical areas.This is due to the instability of regulatory policy, which leads to uncertainty in terms of investment mechanisms. The prevailing trend is to optimize maintenance processes by reducing their costs per turbine as much as possible, especially for processes which are considered routine. This is why this industry often assigns fixed and low sums for machine maintenance costs, which include the reviewing and maintenance of all of the many components of which it is made. As well as electric boards, gearboxes, lifts, oil systems, electronic controls and various safety mechanisms we also have the blades themselves.
Considering the number of parts to maintain and the tight budget for them, as a general rule, any inspection procedure which, although optimal, exceeds the very tight operating costs, is not feasible.
With this in mind, a second principle is analyzed, in this case regarding the civil industrial application of the drone, which asserts that it is not usually feasible to employ aerial technology to substitute something which can be carried out from the ground more cheaply, safely and successfully, unless these three parameters are surpassed from the air, which is usually a complex challenge.
Sector needs
The wind energy industry requires reasoned technical reports that precisely detect, analyze and diagnose the problems and subsequently issue concise recommendations based on the principles of economy and prudence. This data is used to establish a predictive maintenance scheme. Although this could seem simple it is in fact far from it. The consequences of finding a fault in a blade depend in large part on the type of manufacturing process, the model and even the serial number. Faulty parts have been found in which certain symptoms have to be understood on time, in order to avoid a catastrophe. As we have outlined, fault diagnosis of blades is a highly technical task which requires experience and an in-depth knowledge of this extremely specialized product
Digital inspection
This innovative method offers certain advantages for the technicians who have to hang from the blades or the inspection from the ground in terms of safety aspects. It is an advantage not to have to spend as much time with the telescope and certainly in terms of the quality of the data it obtains.
Carrying out a subsequent analysis, based on the images or video captured on site of the entire wind turbine’s surface entails processing huge amounts of data and makes the inspection even more time-consuming. The amount of information obtained in an inspection with RPAS (Remotely Piloted Aircraft Systems) of the wind turbine’s blades, taking pictures of the entire surface with high resolution reflex cameras can vary from 5 to 10 gigabytes of data per machine. This significant and unnecessary increase in information must be filtered and analyzed, which multiplies the number of hours/technicians associated with the inspection. As mentioned above, finding and categorizing blade faults involves specialized engineering work. Minutely analyzing hundreds of high resolution photographs of each wind turbine is not a viable process for this branch of industry. It infringes the first maxim we mentioned earlier, namely that of having an economical inspection procedure.
The main advantages of technology based on drones is that they can provide multisensory measurements and generate high-quality repeatable data.
The processing challenge
The majority of wind turbine blade inspection methods are based on the generation of an on site inspection.
Deciding which faults to highlight and document is up to the inspector’s technical criteria. This means that a qualified inspector has to visit the site, who would otherwise have to review a huge number of photographs or extensive videos, causing a duplication of inspection efforts which is not particularly practical.
This information can be managed through software platforms, in order to automate the management of some of the inspection processes data, in order to transfer it outside of the field. This brings considerable advantages by improving the rigor and objectivity of the inspection. The software platform developed (Web Blade) allows us to solve the processing step by generating comprehensive blade mapping at various levels, measuring and pinpointing the damage with precision, including those elements that are not visible such as deficiencies in the glue lines between internal elements. This disruptive technology has been implemented by Iberdrola and other large companies in the sector, having been applied to the audits of thousands of blades worldwide.
The difficulty of fault diagnosis based on the diverse parameters at play, given that a fault does not have the same level of importance for every blade, reduces the usefulness of automatic detection, although a comprehensive artificial view does allow for a very objective and precise measuring. The experienced eye of the expert engineer is an indispensable guarantee for the wind energy industry as it stands today, and this is backed by the mathematical algorithms that link faults with consequences and facilitate the application of artificial intelligence to the process. This innovative platform allows for an in-depth objective and replicable understanding of the blade’s state, obtained through non-destructive testing carried out at a safe distance, having taken the data from the aircraft. Intelligent and automated analysis helps detect and measure internal and external structural problems, and to analyze and pinpoint faults and relate them to each other, facilitating the comparison of the blades, their progress over time and therefore being able to rank them by risk and current and future maintenance needs. This disruptive procedure, developed in Spain in close collaboration with Iberdrola, which combines drones and software, has recently been validated by VESTAS as a procedure they can apply to their blades.
Having repeatable data of the highest resolution possible, from a high number of good quality sensors, and validated from a technical point of view for diagnosing faults, is an important factor for justifying the advantageous use of this aerial digital inspection platform over other systems.
Rapid and widespread use of drones in civil industry is currently taking place, and they are dominating the skyline of wind energy as valuable allies in the expansion of renewable energies.
Carlos Bernabéu González, Chairman and CEO de Arbórea Intellbird
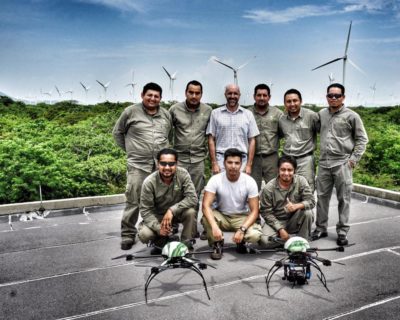
Carlos Bernabéu with the Iberdrola wind energy operations team in La Venta, Oaxaca, México.
Head of Development, manufacturing and commercialization of Aracnocóptero® and of its application in Wind Turbine or Electric power line inspections for large companies in the sector.
He has led aerial inspections in companies such as Endesa, Iberdrola, Enel and Red Eléctrica de España.
– Director of the training school for Remotely Piloted Aerial Systems (SARP) pilots, of Arbórea, the first in Spain. Collaborator at the Spanish Air Force UAS (Unmanned Aircraft Systems) school.
– Head of multiple R+D projects applied to Environmental Management for Public Administrations inside and outside Spain.
– Expert in handling and ethology of birds of prey and management of birds and other invading species vertebrates.
– Speaker and lecturer at diverse national and international congresses organized by Universities and institutions such as UNESCO, NATO and USAL.
– Founder and Chairman of the Spanish Falconry Association (2002/ 2006) and Spanish Representative at the IAF (International Association for Falconry and Conservation of Birds of Prey) (2002/2006)
– Member of the advisory committee of the Ibero American Falconry Archive (www.aic.uva.es) Institute for Ibero-American Studies.
– He has led a number of training initiatives in universities and public institutions well-versed in Environmental management and conservation.
– Advisor of the Drones Excellence Center of the Spanish Aviation Safety Agency (Agencia Estatal de Seguridad Aérea (AESA))
– Author and co-author of publications on RPAS, EIA, Environmental Education, falconry and handling birds of prey, with books and articles in specialized Spanish and international journals.
To find out more about ARBOREA INTELLBIRD: www.aracnocoptero.com
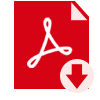