Julia Maria Gomez de Avila Segade | 06/06/2023
The aerospace industry is expanding the use of electrical technologies, as in the case of spacecraft and satellite propulsion. The aim here is to reduce fuel consumption and waste generation; furthermore, the duration of space missions is extended.
Aerospace electric propulsion is a novel system used in space vehicles and satellites that uses electricity to accelerate instead of relying on chemical fuels. Propulsion entails expelling an ionized gas —such as xenon— at high speed and reduces fuel consumption, prolonging space missions.
“Electric propulsion is currently indispensable to ensure the economic viability of commercial satellites in land orbit. For this reason, for the last nine years, the European Commission has funded a research and development program to boost the competitiveness of our aerospace industry,” explains Luis Conde, Professor of Applied Physics at ETSIAE of the Polytechnic University of Madrid.
Main applications of this new technology
The biggest benefit of aerospace electric propulsion has to do with the fact that it is a much more sustainable technology than traditional technologies. This is due to the fact that increases in the exit velocity of the gas and/or plasma drastically reduce the amount of fuel needed, savings that translates into an increase in onboard equipment, such as antennas or transponders.
“It is the only technically possible solution to provide propulsion to the satellites of commercial constellations in low orbit”
In return, this technology is limited by its electrical energy consumption and high currents, which result in very small thrust values compared to traditional engines. However, its propellants can operate uninterrupted for years, so they ultimately deliver a very high total thrust.
“It is the only technically possible solution to provide propulsion to the satellites of commercial constellations in low orbit. Their applications extend as new developments can be deployed on ever smaller satellites,” the expert explains.
Regarding the initiatives that are currently being developed, Conde comments that in Spain there are various groups made up of universities and companies that participate in research and development programs promoted by the European Union.
Among them, Conde highlights several ongoing examples, such as the Crisa company, responsible for the electronics of the Beppi-Colombo mission propellants, or ATD, which is working on cathode technology to operate plasma propellants in space. He also indicates the work of the startup Lenai, which is developing a propellant for microsatellites and nanosatellites.
In addition to the commercial initiatives, it underscores the important academic work carried out by the Polytechnic University of Madrid, which has developed and patented its own plasma propellant, called Alphie, and the Carlos III University, which, in collaboration with the company Sener, is developing the Helicon propellant, based on plasma produced with microwaves.
“In short, electric propulsion in space is a technology that has been established for a long time in telecommunications satellites, and is essential in deep space exploration missions, such as the GOCE or Beppi-Colombo missions,” he admits.
“An electric propellant has to run for very long periods of time”
Challenges to face
The UPM professor points out that the first implementation challenge of this technology is the accumulating of complicated tests necessary for an electric propulsion system to be rated as suitable for orbit use. This process is closely connected to commercial satellite risk assessment by insurance companies.
He also explains that, to verify its reliability, the conditions of space are reproduced as far as possible and the tests are carried out inside a very low-pressure chamber. But due to the fact that an electric propellant has to run for very long periods of time, the tests to verify its operation are complex and long-lasting. “The cost is very high, and the need to simplify and accelerate the qualification processes is currently under debate,” Conde says.
Another major challenge is the technology itself, as this system has very demanding weight, volume, electrical power and reliability requirements, as it requires an electronic power and control unit. “The reduction in production through the standardization of its components, with flexible designs to adapt them to the different types of propellants is one of the objectives of the research program sponsored by the European Commission,” he points out.
Finally, the other technical challenge has to do with the material used, such as propellant. Xenon gas was commonly used due to its high mass and low ionization energy; however, the current geopolitical conflicts have caused its price to skyrocket, which is why alternatives are being sought that can operate with existing propellants and technologies.
Contributor to this article:
Luis Conde, Professor of Applied Physics at the School of Aeronautical and Space Engineering of the Polytechnic University of Madrid.
He has led National and European Plan research projects. He is a member of the European Physical Society and author/co-author of more than 50 research journal articles and 40 papers published at specialized conferences.
As a faculty member, in addition to basic Physics courses, he has taught Plasma Physics to undergraduate and Master’s students in Aerospace Engineering. His current interests are basic plasma physics, diagnostic techniques and plasma thrusters for space propulsion.
Keep reading… Infrared thermal imaging: much more than a pandemic detector
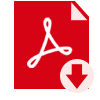