admin | 18/12/2017
GABRIELA REYES DELGADO
Head of Process Safety Aea
PASTORA FERNÁNDEZ ZAMORA
Head of Risks Analysis Area
ANTONIO DÍAZ PÉREZ
Head of Industrial Safety and Reliability Area
ALFREDO RAMOS RODRÍGUEZ
Head of Industrial Safety Department
JUAN SANTOS REMESAL
Director of Industrial Safety Division
Introduction and Background
Industrial regulation, technical standards, design standards and accumulated experience are important guarantees for attaining high levels of safety in the design and engineering of large industrial installations and thereby ensuring operational and business continuity.
Nonetheless, despite complying with regulation and design codes, there is no such thing as zero risk. Industrial installations design and implement safety measures for managing their assets with the twin goals of both reducing the probability of an incident occurring as much as possible and minimizing the associated consequences of any such incident, always seeking to do so in accordance with people safety, the environment and the production and profitability requirements of their investments.
Nowadays, most organizations involved in managing industrial assets put in place rules, standards and procedures which go further than strict legal requirements. They have left behind the early days when accidents were seen as inevitable or to be dealt with after the event. These days it is standard practice to take a proactive approach aimed at preventing and avoiding accidents; industrial asset managers must ensure business continuity throughout the life cycle using tools designed to achieve INTEGRITY across the following three vectors:
Design integrity, applying risk analysis tools which make it possible to produce a design in which the risks are as low as reasonably practical.
Operational integrity, implementing process safety management systems which guarantee the safe operation of assets and safety barriers.
Asset integrity, adopting optimized maintenance and reliability strategies for equipment, infrastructures and safety barriers.
Asset Integrity – Process Safety
This article aims to reflect on each of the previous points, bringing together the key elements, methodologies and tools available to asset managers to apply in order to deliver each organization’s business objectives, as well as the relationship between these tools as illustrated in the appendices. All of this revolves around the concept of SAFETY – in capital letters – as the basis for management and decision making.
Asset Integrity – Process Safety
Designing and engineering industrial processes on the basis of industrial regulation, technical standards, design standards and accumulated experience is crucial for attaining high levels of safety.
Installations must be designed in a way that minimizes risks both on their interior and exterior. The key to this is to undertake an exhaustive analysis and to apply appropriate risk analysis tools to all projects phases where there are possible risk-generating situations.
Each sector makes use of advanced safety criteria, as well as applicable international standards and regulations. The set of tools applied in projects ranges from HAZID/HAZOP studies to SIL Analysis (Assignment of SIL Index, Safety Requirement Specifications or SRS and SIL Verification), LOPA Analysis, Design of Fire & Gas systems, Quantitative Risk Analysis and ALARP, BOW-TIE, Determination of Critical Safety Elements and design standards for these Elements. These risk analysis tools are focused on increasing safety levels and achieving objectives such as:
Identifying external hazards which could affect the interior of the installation.
Identifying internal hazards which could lead to an accident, both due to the hazards associated with the substances present, as well as due to operations in the construction or use of the installation.
Estimating consequences. Quantifying effects and consequences in accordance with the characteristics of the substance capable of generating a risk situation.
Estimating the probabilities of the identified hazard occurring, which allows for an approximation of the overall risk of the installations, once these consequences have been assessed.
Identifying points in the installations which may require design improvements, inspections and maintenance to make the operation safer.
Identifying the zones, installations, equipment and processes which contribute most to risk, with the goal of establishing appropriate mitigation or protection measures to ensure that at all times the risk associated with the establishment is acceptable.
Defining the emergency action strategy and preparing emergency and contingency plans.
Various different tools can be used depending on the particular engineering phase, the project being developed, the end objective and the risk management policy which the project developer and engineering have defined as being appropriate for attaining these objectives. Applying these tools facilitates the attainment of significant safety benefits throughout the life cycle of an industrial installation.
By way of reference, the following table aims to identify the most suitable risk analysis tools for the different project phases depending on the expected results. The attached chart sets out the main applications within the safety life cycle stage of an activity.
FASE DEL PROYECTO | MÉTODO ANÁLISIS DE RIESGOS | RESULTADOS ESPERADOS |
---|---|---|
INGENIERÍA CONCEPTUAL | HAZID CHECKLIST WHAT IF | Orientación para la selección del proceso. Detectar peligros inaceptables de proceso. Ayuda para el diseño del proceso. Identificar modificaciones fundamentales en el proceso que reduzcan el nivel de riesgo. Ayuda a la localización geográfica del proyecto. |
INGENIERÍA BÁSICA | HAZID CHECKLIST WHAT IF FMEA HAZOP | Identificar con mayor detalle peligros en el proceso seleccionado y en el diseño propuesto; riesgos asociados a la localización geográfica; riesgos sobre equipos especiales o críticos en el proceso. |
INGENIERÍA DE DETALLE | CHECKLIST WHAT IF FMEA HAZOP SIL/VERIFICACIÓN Y SRS QRA FHA o EAC RAMS EERA SVA |
Identificar todas las situaciones de peligro en el proceso, valorando los riesgos asociados. Detectar aspectos de la operación no contemplados inicialmente. Ayudar a establecer los procedimientos de operación, comisionado y puesta en marcha. |
PLANTAS EN OPERACIÓN | CHECKLIST HAZOP SIL/VERIFICACIÓN Y SRS FHA o EAC QRA RAMS EERA SVA |
Garantizar la operación y que la información sobre calidad, requisitos legales, seguridad de proceso y procedimientos operativos es completa y esta actualizada. Incorporar las lecciones aprendidas en accidentes o incidentes recientes y valorar la incorporación de nuevos equipos, sistemas y tecnologías que mejoren los niveles de seguridad |
Safe design and technical integrity
Safety Line Cycle – Tools and solutions
Operational Integrity. Process Safety Management (PSM) System
Un Sistema de Gestión de Seguridad de Procesos, o PSM por su acrónimo en inglés, tiene como objetivo principal evitar la materialización de accidentes en aquellas instalaciones donde se utilicen, almacenen, produzcan y/o manipulen sustancias con características peligrosas y su consecución se soporta en dos pilares fundamentales como son el Compromiso de la Organización con la seguridad y el Conocimiento y Gestión de los riesgos asociados a los procesos.
The main objective of a Process Safety Management (PSM) System is to avoid accidents occurring in installations where hazardous substances are used, stored, produced and/or manipulated. This is achieved on the basis of two essential pillars: Organizational Commitment to safety and Knowledge and Management of the risks associated with the processes.
PSM: ENERGY INSTITUTE
BLOQUE | ELEMENTOS |
---|---|
Liderazgo en Seguridad de Procesos | 1.Liderazgo, compromiso y responsabilidad. 2.Identificación y cumplimiento de la legislación vigente y de las normas de la industria. 3.Selección de personal, contratación y competencias y aseguramiento de seguridad y salud. 4.Participación del personal. 5.Comunicación con las partes interesadas. |
Identificación y Evaluación de Riesgos | 6. Identificación de peligros y evaluación de riesgos. 7. Documentación, registros y gestión del conocimiento. |
Gestión de Riesgos | 8. Manuales de operación y procedimientos. 9. Seguimiento de las variables operativas y relevos. 10. Gestión de interfaces operativas. 11. Normas y prácticas. 12. Gestión de cambios y gestión de proyectos 13. Disponibilidad de la operación y puesta en marcha de los procesos. 14. Preparación para emergencias. 15. Inspección y mantenimiento. 16. Gestión de los elementos críticos para la seguridad. 17. Control del trabajo, permisos de trabajo y gestión del riesgo de las tareas. 18. Contratistas y proveedores, selección y gestión. |
Revisión y Mejora | 19. Informes de Incidentes e investigación. 20. Auditoría, garantía, revisión de la gestión e intervención |
PSM – PROCESS SAFETY
GOOD PRACTICE: ENERGY INSTITUTE
Within the life cycle of installations, the PSM addresses aspects and issues related to:
Safedesign, engineering and construction.
Hazardassessment.
Efficient alarms.
Effective process control.
Appropriate procedures for putting in place and operating installations.
Management of modifications.
Inspection, testing and maintenance of equipment.
Staff training.
Relationships with providers and suppliers.
Communications in the organization and between its managers.
Thus, an appropriately designed and implemented PSM – comprehensively covering the above aspects, adapted to each organization’s reality and formulated under the safety prism – helps:
Foster a safety culture.
Identify, assess and appropriately manage the installation’s risks.
Identify and manage critical safety elements in installations.
Establish procedures and necessary measures for process control.
Guarantee the maintenance and inspection of installations.
Ensure professionals are appropriately trained and congruent with process safety at all levels and in all areas of the organization.
Analyze and manage the impact on safety of technical and organizational change processes.
Analyze and manage the impact on safety of technical and organizational change processes.
Investigate the causes of accidents and incidents and put in place the measures to avoid them repeating in the future.
Manage systematically and in a standardized way all aspects contributing to the safety level among installations or businesses in the same Group.
Attaining some of the following benefits:
ImprovingAssetManagement and the safety levels of installations.
Increasing installations’ readiness and production levels.
Reducing repair, loss of earnings and insurance costs.
Aligning the organization with the achievement of business objectives.
Ensuring compliance with legislative requirements.
Reducing the exposure to large scale financial losses,lawsuits, sanctions and public liability.
Improvinginsurance premiums.
Enhancing the company’s corporate image both internally and externally, plus other intangible benefits.
Asset Integrity. Asset Integrity
The internationally applied concept of ASSET INTEGRITY relates to practices, methodologies and management techniques in relation to asset integrity aimed at optimizing the combined use/risk/value of assets.
The use of any machinery, equipment or, ultimately, any industrial asset involves a degree of wear and tear, but at the same time it is the (direct or indirect) source of value creation (income). Use results in a degree of depreciation, with the remaining working life of the asset reducing with each use; but asset degradation does not only have economic effects, it also has safety implications and accordingly operational risks and the integrity of the asset itself will also be affected over time.
One of the most common mechanisms for managing asset integrity at the industrial level is industrial maintenance of various forms (preventative, predictive, corrective, etc.) but in addition to these “static” techniques a series of advanced techniques have been developed in recent years to optimize combined Use/Risk/Value.
All of these techniques can be encompassed under a global strategy for Asset Management Integrity developed under the ISO 55,000 standard, which sets out techniques for optimizing: the reliability/readiness/care of industrial installations (RAM); the reliability of machines and dynamic equipment (RCM); and the physical integrity of equipment (RBI).
The requirements set out in the ISO 5500X standards provide a structured approach to developing an asset management system which facilitates the achievement of the organization’s objectives and provides necessary controls to ensure delivery.
This standard has helped provide a structure in response to an industry need spurred by developments in the maturity of organizations and complex external environments and situations in which the business can find itself impugned by accidents such as the Mexican Gulf (Macondo, BP). This is illustrated in the following chart:
Investment management is performed using a Life Cycle concept in which the relationship between operating costs and risk or reliability taken on vital importance. The ongoing comparison between competing investment scenarios has become a daily exercise and is fundamental for business decision making.
Conclusions
Various different tools are available to industrial companies according to the particular activity phase, the project being developed, the end objective and the risk management policy which the company has established for attaining its safety objectives.
A proactive approach aimed at preventing and avoiding accidents is standard practice. Managers of industrial assets must ensure business continuity throughout the life cycle using tools aimed at achieving design and operational INTEGRITY, as well as integrity in terms of asset readiness and reliability.
A coordinated and integrated application of the set of tools described in this article allows for significant safety benefits to be obtained throughout the life cycle of an industrial installation. Selecting the right tools requires experience in order to identify those which are the best fit for the installation being assessed and the desired objectives.
In this regard, INERCO has over 30 years of experience advising on risk management and enhancing integral safety levels in the industrial sector (oil & gas, chemical, energy, mining, metals, industrial engineering, etc.), employing the most cost effective approaches to reducing risk.
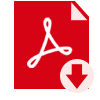